SAP Articles
SAP Project Failing? The Quality Gate Secrets Nobody Tells You
Noel DCosta
- Last Update :
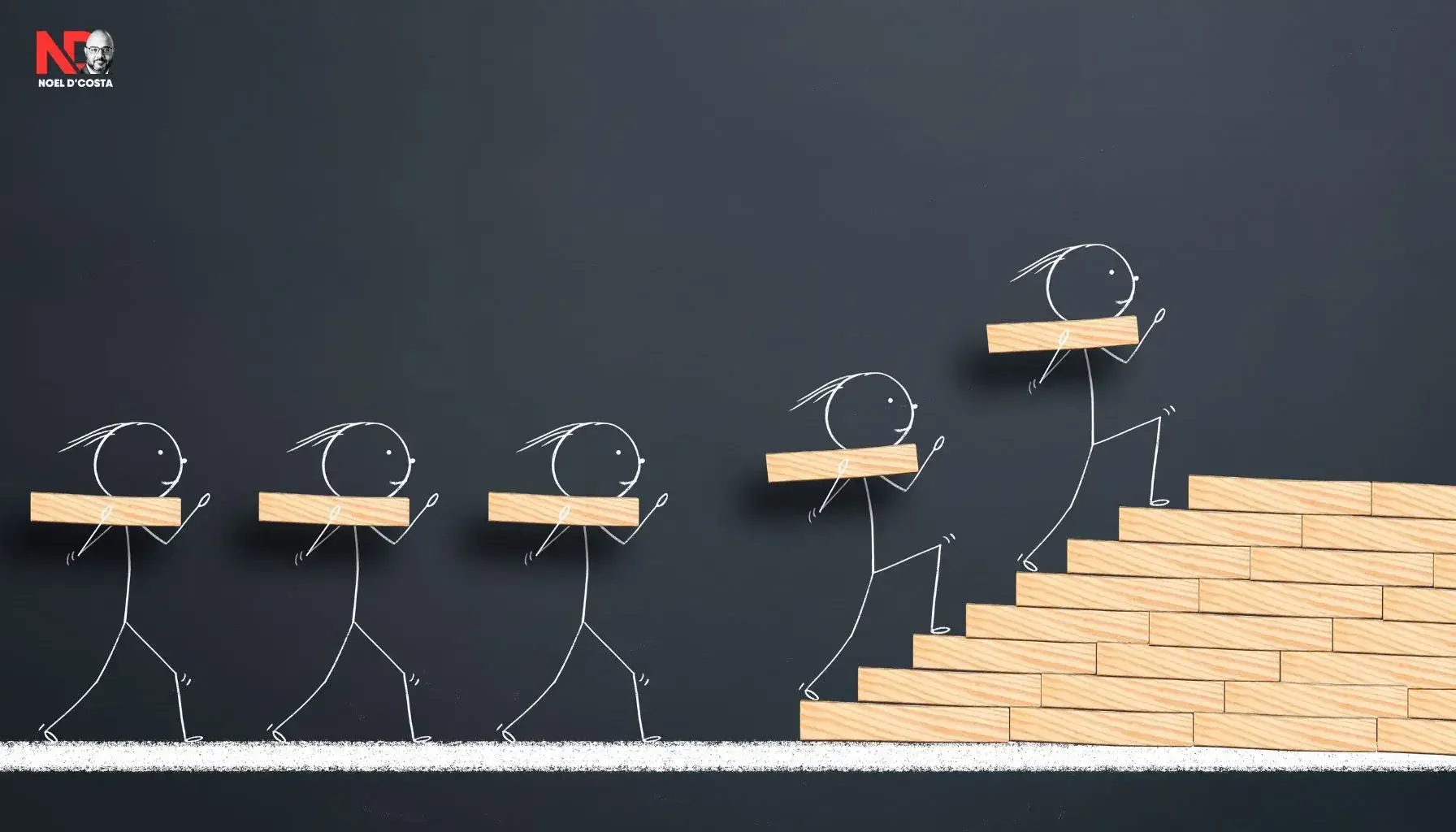
Did you know that skipping quality checks in an SAP implementation can lead to delays, broken processes, and unexpected costs? That’s why I think SAP Quality Gates Implementation is essential. These checkpoints make sure each phase meets quality standards before moving forward.
You have to think of quality gates like stopping at a traffic light. Before jumping from blueprinting to development or testing to go-live, everything has to get a deeper look. I tell clients without hesitation – if it passes, great, keep going. If not, fix the problems before they blow up later. Your project needs these controls.
Without these checks, little errors pile up fast. A missed requirement in the blueprint phase can destroy your processes down the road. I’ve seen this happen countless times. Quality gates catch mistakes early when they’re still cheap to fix. Your team won’t be stuck fixing emergencies at 2am after launch.
They also keep people honest. Instead of the mad dash at the end, teams focus on doing good work at every step. I don’t budge on this with clients. It makes deployments smoother and gives you a system that actually works after go-live. Your business operations depend on getting this right.
A Lesson based on my Experience
One major consumer goods company in Singapore was rolling out SAP globally. The team rushed through testing to hit deadlines. I watched this disaster unfold. User testing barely happened, but executives pushed for the launch anyway. Within days, problems started showing up e.g. missing setups, broken workflows, data completely wrong.
The problem was that they didn’t have structured quality gates. Nobody checked the work properly at key points. The team scrambled to fix live system issues that should’ve been caught months earlier. This caused weeks of post-launch chaos and one furious client. Your project could easily end up the same way.
I never skip quality gate reviews. No shortcuts. No rubber stamps. Every stage gets proper sign-off. Yeah, it takes more time upfront, but saves months of cleanup later. If you want an SAP project that works, quality gates aren’t optional—they’re non-negotiable. I’ve cleaned up too many messes to say otherwise.
Quality gates must have specific, measurable acceptance criteria that everyone agrees to before the project begins. Executive sponsors need to understand and publicly support the quality gate process to prevent shortcuts when deadlines approach.
10 Key Takeaways on SAP Quality Gate Implementation
- Quality gates catch problems when they’re cheap to fix, not after they’ve crashed your system.
- Skip the quality checks and you’ll pay three times as much fixing the mess later.
- Your blueprint phase needs thorough review – mistakes here wreck everything downstream.
- Testing isn’t just a box to check – it’s your last defense against a failed go-live.
- Document every approval so when someone asks “who signed off on this?” you’ve got answers.
- Clear quality gates stop the blame game – everyone knows their responsibilities.
- Executives hate delays, but they hate failed implementations way more.
- Each quality gate needs real criteria – not just “looks good to me” rubber stamps.
- Project managers who rush past quality gates usually aren’t around for the cleanup.
- Quality gates build confidence throughout the organization – from users to leadership.
Quality gates aren’t about slowing things down. They make sure you don’t waste time fixing avoidable problems.
What Are SAP Quality Gates?

I believe SAP Quality gates keep SAP Projects from going away from its intended goals. Teams must prove they did their work right before moving to the next phase. These checkpoints catch mistakes early, before they turn into expensive nightmares down the road.
Think of quality gates like airport security. If your project deliverables pass inspection, you move ahead. If not, you go back and fix it before boarding. Skip these checks? You’ll be halfway across the ocean when you realize something important is missing.
Without quality gates, everything gets rushed. Testing isn’t thorough. Problems stack up, and fixing them after go-live costs a ton of money. With them, you know who’s responsible for what, get fewer nasty surprises, and end up with a system that actually works.
Each gate has specific entry and exit requirements—teams must show their test results, approvals, or finished tasks before moving forward.
How SAP Quality Gates Work
- Blueprint Approval – Makes sure business requirements aren’t missing anything.
- Design Validation – Checks that configurations actually match what the business needs.
- Development Sign-Off – Verifies that customizations and integrations work properly.
- Testing Review – Makes sure key processes actually work right.
- Go-Live Readiness Check – Confirms the system won’t crash on day one.
Skip quality gates, and your project turns into a disaster. Errors everywhere, blown deadlines, and budgets that spiral out of control. Stick to the process, and you stay in charge.
Do You Really Need an SAP Quality Gates Implementation?

Yes, you do.
I believe skipping SAP Quality Gates Implementation is like skipping a car inspection before a cross-country road trip. You might save time upfront, but when the engine dies in the middle of nowhere, you’ll wish you hadn’t.
Quality gates force you to stop and check your work. No assumptions. No “we’ll fix it later” nonsense. Everything is tested, reviewed, and signed off before moving forward.
I’ve seen what happens when people ignore this:
- Bugs start building up until half the system doesn’t work.
- Testing becomes inadequate because everything’s rushed.
- Deadlines get pushed again and again because issues pile up.
- Everyone blames each other instead of fixing the real problem.
And when teams actually use quality gates?
- Mistakes get caught early, before they cost millions.
- Testing is thorough, so users don’t find disasters on day one.
- Timelines stay on track, because problems aren’t left for the last minute.
- People take ownership, instead of throwing problems over the fence.
I’ve seen SAP projects go away from intended goals because someone wanted to skip a few “extra steps.” Those same steps could have saved months of pain.
So, do you need them? Ofcourse you do! There is no two ways about it.
Key Benefits of SAP Quality Gates

So, when clients ask me about SAP Quality Gates, I tell them they’re not optional extras. They’re essential project safeguards. Look, I’ve seen projects with quality gates succeed brilliantly and those without crash and burn.
- Quality gates catch problems early – They spot issues when they’re cheap and easy to fix. I worked with a manufacturing company whose quality gate review caught a critical integration flaw during design. Fixing it then cost them a week. Finding it after go-live would have shut down production for a month. That’s real money saved.
- But they require real commitment – Half-hearted quality gates are useless. One retail client did “reviews” that were basically rubber stamps. Six months in, they were hopelessly behind schedule because nobody addressed the issues these fake reviews should have caught. That’s like installing smoke detectors without batteries. Just pointless.
- They create clear accountability – Everyone knows who’s responsible for what, and when. I brought in quality gates for a client whose project was a blame-game nightmare. The structured sign-offs forced team members to own their deliverables, and suddenly things started getting done. It was night and day difference.
- But they need executive backing – Without leadership support, quality gates get skipped when schedules tighten. I watched one company push past critical quality checks to meet an arbitrary deadline. Their go-live was a total disaster that cost three times what the proper reviews would have. Complete waste of money.
- They improve documentation – Each gate requires proper sign-off on completed work. One pharmaceutical client’s quality gates ensured thorough documentation at every phase. When they had staff turnover, the new team could pick up where others left off without starting over. Saved them months of rework.
- The real benefit is project confidence – Whoever’s paying for the project gets proof it’s being done right. I’ve seen more projects fail from cutting corners than from following the process. It happens all the time.
The best approach is to take quality gates seriously. Staff them with people who’ll say “no” when needed. Schedule them properly. And remember – every hour spent on quality reviews saves days or weeks of cleanup later. Otherwise, you’re just gambling with your project’s success. I’ve cleaned up too many messes to think otherwise.
Critical SAP Reads for Smarter Business Decisions
How to Design an Effective SAP Quality Gate Framework Based on SAP Activate

So, when setting up quality gates for SAP Implementation projects, I always start with SAP Activate methodology as the foundation. This isn’t about reinventing the wheel – SAP’s already mapped out the critical checkpoints. But you’ve got to adapt them to your project’s specific needs.
- First, align your quality gates with SAP Activate’s phases – Prepare, Explore, Realize, Deploy, and Run. Each phase needs its own quality gate that must be passed before moving forward. I had a client try to combine phases to “save time” – complete disaster. They ended up redoing weeks of work.
- For each gate, define specific entry and exit criteria. And I mean specific – not “testing complete” but “95% of test cases executed with 100% of high-priority defects resolved.” One manufacturing client’s quality gates failed because the criteria were too vague. Nobody knew if they’d actually passed or not.
- Document everything in your project charter right from the start. Make sure executives sign off on the framework before the project kicks off. I’ve seen too many projects where quality gates got skipped because leadership didn’t understand their importance until it was too late.
- Assign clear ownership for each quality gate. Someone must be responsible for confirming criteria are met, and they need authority to delay the project if standards aren’t met. One retail client appointed a senior director as quality gate owner – when he said “not ready,” everyone listened.
- Include business users in your quality gate reviews, not just the IT team. Their sign-off is crucial, especially for process validation. A logistics client caught major workflow issues because warehouse managers were part of their quality gate team.
The key thing is don’t treat quality gates as flexible. They’re non-negotiable project milestones. When timelines get tight, quality gates are often the first thing cut. I’ve never seen that end well. Every single time, the project paid for it later with interest.
SAP Activate Quality Gates Framework
Phase & Quality Focus | Deliverables & Approval Criteria |
---|---|
Discover Quality Focus: Business case validation, stakeholder engagement assessment. |
Deliverables: Business case document, project vision, high-level roadmap. Approval Criteria: Signed-off business case, executive buy-in, high-level requirements documented. |
Prepare Quality Focus: Governance setup, resource allocation, risk assessment. |
Deliverables: Project charter, governance framework, risk register. Approval Criteria: Project charter approval, risk mitigation plan, team onboarding completed. |
Explore Quality Focus: Fit-gap analysis, process design, backlog prioritization. |
Deliverables: Fit-gap report, business process diagrams, integration architecture. Approval Criteria: Approved fit-gap report, defined business processes, validated integration approach. |
Realize Quality Focus: Configuration validation, integration testing. |
Deliverables: Configured system, test cases, defect resolution reports. Approval Criteria: Passed unit and integration tests, minimal critical defects, user acceptance sign-off. |
Deploy Quality Focus: Data migration validation, cutover readiness. |
Deliverables: Data migration reports, training completion logs, cutover plan. Approval Criteria: Successful migration testing, training effectiveness validated, go-live checklist completed. |
Run Quality Focus: Post-go-live monitoring, system stabilization. |
Deliverables: System performance reports, issue logs, improvement roadmap. Approval Criteria: Stable system performance, minimal high-priority incidents, operational handover completed. |
Step-by-Step Process to Implement SAP Quality Gate Framework
Look, implementing SAP Quality Gates isn’t complicated, but it takes discipline. Here’s how I’ve done it successfully with clients who actually wanted their projects to succeed. I’ve seen SAP projects that looked great on paper but turned into disasters because nobody stopped to check the work along the way.
- Start by mapping your quality gates to your project methodology. If you’re using SAP Activate, align gates to the end of each phase – after Prepare, Explore, Realize, and Deploy. One energy client tried creating random checkpoints and ended up with a mess. Stick to natural project breakpoints.
- Next, define what “done” means for each gate. Be specific and measurable. For the Explore phase gate, you might require “100% of business processes documented and signed off by process owners.” I worked with a manufacturing client who created detailed checklists for each gate – saved them from countless arguments later.
- Then, build these gates into your project schedule with fixed dates. Don’t just say “we’ll have a quality gate sometime after testing.” Put it on the calendar. Include buffer time before each gate for fixing issues. One of my retail clients allocated a full week before each gate just for cleanup. Smart move.
- Assign the right people to each gate review. You need business stakeholders, technical leads, and project management at minimum. And make sure someone has veto power – the authority to say “we’re not ready to move forward.” I saw one project crash because nobody had the power to delay the next phase even though they weren’t ready.
- Create simple templates for gate reviews. Document what’s being reviewed, who’s reviewing it, what standards must be met, and what the results are. Keep track of these documents throughout the project. They’re your evidence that things were done right.
- Finally, make quality gates visible to everyone. Display the criteria and results where the whole team can see them. One client put their quality gate dashboard on the wall of their project room. Made it impossible to ignore or forget.
- Most important – stick to your guns. Quality gates work only if they’re mandatory. The minute you start making exceptions, the whole framework falls apart. I’ve seen it happen too many times.
Step-by-Step Process to Implement SAP Quality Gates with Solution Manager

Implementing SAP Quality Gates with Solution Manager gives you built-in tools to enforce quality. Here’s how I’ve helped clients set this up properly.
- First, activate the Project Management module in Solution Manager. Many clients skip this, thinking they’ll just use their own tools. Big mistake. Solution Manager tracks everything in one place – requirements, configurations, test cases, and defects. One manufacturing client who tried using separate systems for everything ended up with massive inconsistencies.
- Next, set up your project structure in Solution Manager to match your implementation phases. Make sure each phase has clear milestones that align with your quality gates. I worked with a retail client who carefully mapped their project roadmap in Solution Manager – made tracking progress dead simple.
- Then, define your quality gate criteria directly in Solution Manager. Use the KPI framework to establish measurable thresholds for each gate. For example, “98% of test cases executed with less than 5% failures.” My utility sector client created detailed scorecards for each gate – no more debates about whether they’d met the standard.
- Configure automated status reporting from Solution Manager. This pulls real data instead of relying on what people claim is done. One of my clients discovered through Solution Manager reports that 40% of their “completed” test cases hadn’t actually been executed. Caught it before the quality gate, not after.
- Set up defect management workflows that link directly to your quality gates. Solution Manager can track whether critical issues are resolved before allowing a gate to pass. A healthcare client used this to prevent progression until all compliance-related defects were fixed.
- Create gate review templates within Solution Manager’s document management. Store all evidence and sign-offs in the system. When auditors came knocking at my financial services client, they pulled everything from Solution Manager in minutes.
- Most important – train your team to use Solution Manager properly. It’s powerful, but only if people actually use it. Don’t let team members keep working in spreadsheets. I’ve seen projects where Solution Manager became just another place to update status rather than the central project tool it should be.
Common Challenges in SAP Quality Gates Implementations

I’ve seen a lot of SAP projects stumble with quality gates. Look, here’s what typically goes wrong in the real world.
- When projects get delayed, the first thing customers do is kill quality gates or have them rushed or skipped. Reviews then become rubber-stamp exercises. Their go-live was a nightmare – systems crashed, orders got stuck, they rolled back completely. The three weeks they “saved” cost them three months of recovery. Total disaster.
- Unclear gate criteria create constant problems. Ambiguous statements like “testing complete” or “configuration done” start arguments about what “done” actually means. I worked with a retail client whose quality gate simply stated “UAT completed.” Half the team thought that meant “all tests executed” while others thought it meant “all defects fixed.” I asked their teams to update the status with meaningful responses.
- Leadership commitment drops fast. Executives love quality gates until they interfere with arbitrary deadlines. One CIO overruled a failed quality gate to meet a quarterly target. The resulting issues cost twice what delaying would have. I’ve seen this pattern repeat so many times.
- Resource constraints make quality gates fail. When key people work multiple projects, proper reviews suffer. Some clients schedule thorough gate reviews but assigned the same three people to evaluate everything while handling their regular jobs. Reviews became superficial. Just checking boxes, really.
- I’ve seen documentation issues happen quite a lot. If deliverables lack proper documentation, reviewers can’t assess them. Development team claimed 95% completion, but can’t produce evidence during the quality gate. Quality Gates fail, causing weeks of delay while documentation caught up. Completely avoidable situation.
- Cultural resistance remains the hardest obstacle to overcome. Teams used to rushing through milestones hate quality gates. I’ve watched project managers try everything to bypass gates rather than meet standards. Changing that mindset is harder than implementing the technical framework. But trust me, it’s worth the effort.
Challenges and Strategies for SAP Quality Gates Implementation
Challenges | Strategies |
---|---|
Undefined Quality Criteria at Each Gate | Establish standardized quality checklists, define clear acceptance criteria, and document gate approval processes. |
Resistance to Quality Gate Reviews | Educate stakeholders on the benefits, integrate quality gates into project governance, and enforce accountability. |
Delays in Quality Gate Approvals | Automate approval workflows, set predefined timelines for gate reviews, and implement escalation procedures. |
Inconsistent Application Across Teams | Develop a unified SAP Quality Gate framework, conduct regular training, and ensure adherence through audits. |
Inadequate Test Coverage Before Gate Approval | Mandate regression, performance, and security testing before gate clearance, and enforce automated test validation. |
Lack of Integration with Project Milestones | Align quality gates with SAP Activate phases, incorporate them into project plans, and link approvals to milestone completion. |
Failure to Address Defects Before Progressing | Implement a strict defect resolution policy, track unresolved issues, and block gate approvals for critical defects. |
Insufficient Executive Sponsorship | Secure leadership buy-in, provide transparency on quality impact, and integrate quality reporting into project dashboards. |
Over-Reliance on Manual Checks | Leverage SAP Solution Manager for automated quality gate monitoring and enforce digital approvals. |
Poor Documentation of Gate Decisions | Maintain detailed audit trails, require formal sign-offs, and store all gate approval records in a central repository. |

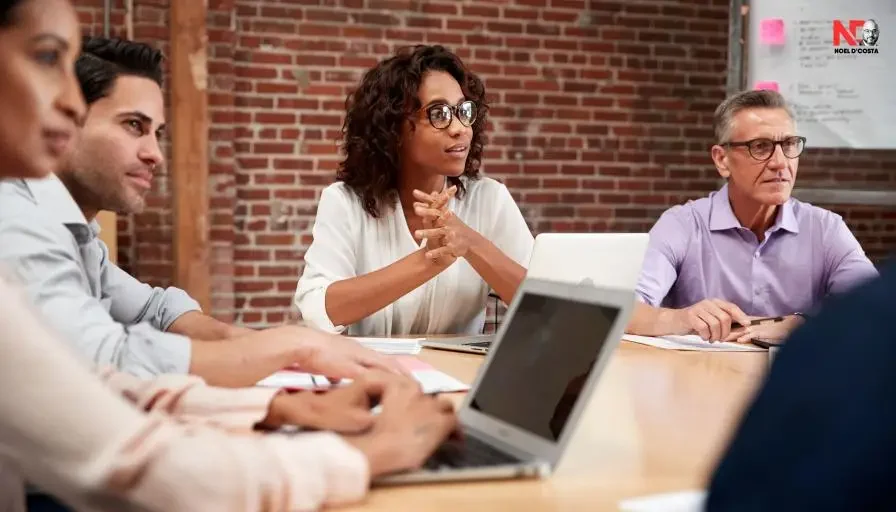
Third-Party Tools for an SAP Quality Gates Implementation
I’ve seen a lot of companies try to run SAP quality gates with spreadsheets and emails. Look, that approach falls apart fast when projects get complex. Here are some tools that actually work in the real world.
1. JIRA and Confluence
Jira and Confluence work great together for quality gate management. Jira tracks all your requirements, tasks, and defects while Confluence stores your gate criteria and evidence. One consumer goods client used this combo to manage gates across a global rollout. They created quality gate dashboards that showed real-time status. Made a huge difference in visibility.
2. Microsoft DevOps
Microsoft DevOps (formerly TFS) is another solid option if you’re a Microsoft shop. The work item tracking and approval workflows fit quality gates perfectly. I worked with a manufacturing client who integrated it with SAP Solution Manager. Their quality gates pulled test results directly from SAP and showed them in DevOps dashboards. Super effective.
3. Tricentis Tosca
Tricentis Tosca helps tremendously with test-related quality gate criteria. It tracks test coverage and execution status, which feeds directly into your quality gate decisions. A healthcare client used it to enforce their rule that no quality gate could pass with less than 95% test coverage. Found some serious gaps that would’ve slipped through.
4. Service Now
ServiceNow works well if you’re already using it for IT service management. The workflow engine handles quality gate approvals smoothly. A financial services client extended their ServiceNow implementation to manage all quality gate sign-offs. Everything was documented and timestamped, which their auditors absolutely loved.
5. Micro Focus ALM
Micro Focus ALM/Quality Center remains popular for quality gates in larger SAP implementations. It manages requirements, test cases, defects, and releases in one place. An energy sector client used it to enforce traceability across all quality gates. Every requirement had to trace to test cases and show successful execution.
6. SharePoint
Don’t forget about good old SharePoint if you need something simpler. Custom lists with approval workflows can manage basic quality gates effectively. Just make sure you build in reporting capabilities. One retail client created a clean SharePoint quality gate solution that worked beautifully for a mid-sized implementation.
Third-Party Tools for SAP Quality Gates Implementation
Tool | Role in Quality Gates | SAP Integration | Strengths | Limitations |
---|---|---|---|---|
Jira & Confluence | Tracking issues & sign-offs | Indirect (API-based) | Agile, audit trails, collaboration | No native SAP traceability |
Azure DevOps | Pipeline & task approvals | Custom via APIs | Traceability, DevOps flow | Needs process mapping |
Tricentis Tosca | Test automation for gates | Certified SAP support | Scalable, risk-based tests | Requires alignment effort |
ServiceNow | Approval workflow control | Via adapters/ChaRM | Audit-ready, ITSM integration | Config-heavy for SAP |
Micro Focus ALM | Test & defect governance | Via middleware | Mature test planning | Heavy setup |
SharePoint | Docs & checklist mgmt | Manual only | Familiar UI, versioning | No SAP process linkage |
SAP Solution Manager | Native change mgmt & gates | Direct | Full lifecycle control | Complex to deploy |
SAP Cloud ALM | Cloud-native gate tracking | Native | Lightweight, fast setup | Still maturing |

Measuring the Success of SAP Quality Gates
A quality gate isn’t just a meeting—it’s a checkpoint to catch issues before they turn into expensive problems. If you want to know whether your SAP Quality Gates Implementation is working, look at these three metrics.
1. Defect Leakage Rate
Formula:
What it means:
This tells you how many issues slipped past all your quality gates and made it to production. If this number is high, your testing and approval process isn’t catching enough problems early.
Example: If 200 defects were found during testing and another 50 popped up after go-live, your Defect Leakage Rate is 20%. That’s too high. A strong quality gate process should keep this below 5-10%.
2. Quality Gate Pass Rate
Formula:
What it means:
This measures how often teams pass quality gates on the first attempt. If this number is too high (near 100%), it likely means people aren’t checking things properly. If it’s too low (under 50%), teams might not be prepared when they reach a gate.
Example: If a project has 10 quality gates and teams pass 9 of them on the first try, the pass rate is 90%. That sounds good, but if no gate ever fails, it could mean approvals are just being rubber-stamped.
3. Go-Live Incident Rate
Formula:
What it means:
This shows how stable the system is after go-live. If users are constantly raising tickets, it means quality gates didn’t catch enough real-world issues. A low incident rate means the system is actually working as expected.
Example: If a company has 5,000 transactions per day and gets 250 incident tickets in the first month, the Go-Live Incident Rate is 5%. If this number is too high, it usually points to rushed testing or missed requirements.
If these three numbers look bad, your quality gates aren’t working. If they look good, your SAP project will be a lot smoother—and a lot less stressful.
Steps to Measure Success:
- Define KPIs: Track metrics like defect resolution rates, compliance scores, and cost savings.
- Analyze Outcomes: Review gate performance using detailed reports and identify areas for improvement.
- Act on Findings: Adjust criteria, tools, or team processes based on recurring issues.
- Leverage Lessons Learned: Apply insights from successful projects to strengthen your framework.
- Communicate Results: Share performance data with stakeholders to reinforce accountability and trust.
Measuring success isn’t just about numbers; it’s about using data to drive better decisions and outcomes. With the right approach, your SAP Quality Gates can become the backbone of a reliable, high-performing project framework.

Conclusion
I believe SAP Quality Gates can transform implementations from disasters into success stories. If you treat these Quality Gates beyond another checkbox, you will see their value.
By building them into your project, each phase hits its targets and matches what the business needs. Good quality doesn’t happen by accident.
When I’ve managed SAP projects, planning and follow-through made all the difference. I messed up a few times early on, learned the hard way.
What works is setting exact quality criteria, using Solution Manager properly, and getting the right people involved in reviews. These gates reduce risks, save resources, and give teams clear direction at every step.
I think you should use SAP Quality Gates as a competitive advantage. They create accountability, build confidence with executives, and deliver real results like saving money and finishing on time.
Have you used Quality Gates in your projects? I’d like to hear about your experiences—what worked, what failed, how you fixed problems when they came up. If we share what we’ve learned, more implementations will succeed.
Start improving your Quality Gates now and set your SAP project up for success!
If you have any questions, or want to discuss a situation you have in your SAP Implementation, please don't hesitate to reach out!
Frequently Asked Questions
1. What is a quality gate in SAP?
A quality gate in SAP is a predefined checkpoint during an SAP implementation where specific criteria must be met before the project can move to the next phase. It ensures deliverables meet quality and compliance standards.
- Purpose: Quality gates verify that milestones like system configuration, testing, or data migration are completed to the required standard.
- Example: Before transitioning from the Realize phase to the Deploy phase in SAP Activate, a quality gate ensures that integration testing is complete, and all critical issues are resolved.
Quality gates reduce risks and improve the likelihood of project success.
2. What are the different types of quality gates in SAP projects?
Quality gates in SAP projects cover various aspects of the implementation lifecycle:
- Configuration Quality Gate: Checks system design and configurations before testing.
- Testing Quality Gate: Verifies completion of unit, integration, and user acceptance testing.
- Data Migration Quality Gate: Ensures data is cleansed, validated, and successfully loaded.
- Go-Live Quality Gate: Confirms readiness for deployment, including training and support plans.
Example: A data migration quality gate ensures legacy data is accurately mapped and uploaded into SAP S/4HANA before testing.
3. What are the quality gates in the SDLC for SAP projects?
Quality gates in the Software Development Life Cycle (SDLC) for SAP projects ensure smooth transitions between stages like design, development, and deployment.
- Requirements Gate: Verifies business requirements align with SAP capabilities.
- Development Gate: Confirms custom developments are complete and meet technical standards.
- Testing Gate: Assesses testing completeness and defect resolution before moving forward.
Example: During SAP custom development, a quality gate might require all enhancements to pass performance testing before integration.
4. What is the quality gate rule in SAP?
The quality gate rule in SAP refers to the predefined criteria or standards that must be met before a project phase can proceed. These rules ensure compliance, quality, and alignment with business objectives.
- Implementation: Rules are established during project planning, focusing on areas like system readiness, testing completeness, or data accuracy.
- Example: A rule might state that all critical defects found during integration testing must be resolved before moving to the Deploy phase.
Quality gate rules create accountability and keep the project on track.
5. How are quality gates applied in SAP testing?
Quality gates in SAP testing evaluate whether the system meets performance, functionality, and user expectations before advancing to the next stage.
- Unit Testing Gate: Verifies individual modules work as intended.
- Integration Testing Gate: Confirms different SAP modules and third-party systems work together seamlessly.
- User Acceptance Testing (UAT) Gate: Ensures end-users approve the system for deployment.
Example: An integration testing gate might check that SAP Finance integrates properly with SAP Sales and third-party banking systems.
6. Can you provide examples of quality gates in SAP?
Here are common examples of quality gates in SAP projects:
- Blueprint Quality Gate: Ensures the SAP solution blueprint aligns with business requirements before configuration begins.
- Data Migration Gate: Validates data accuracy and readiness for migration into SAP S/4HANA.
- Go-Live Gate: Confirms all critical activities, such as end-user training and final testing, are complete before the system goes live.
Example: A Go-Live quality gate might include checks for user readiness, backup plans, and stakeholder approvals.
7. What is a quality gate in the SAP manufacturing process?
In SAP’s manufacturing modules, a quality gate ensures product quality at critical points in the production process.
- Purpose: To detect and address defects early, ensuring compliance with quality standards.
- Example: In SAP QM (Quality Management), an in-process quality gate might inspect semi-finished goods before moving to the next production stage.
These gates integrate seamlessly with SAP systems to improve product quality and reduce waste.
8. How are quality gates used in SAP project management?
In SAP project management, quality gates are checkpoints that evaluate progress and quality before advancing phases.
- Examples:
- Realize Phase Gate: Ensures system configuration and integration testing are complete.
- Deploy Phase Gate: Confirms readiness for data migration, end-user training, and cutover activities.
Example: During an S/4HANA implementation, a quality gate in the Deploy phase might confirm that all data migration plans and backup systems are validated.
9. How do quality gates work in SAP automotive industry projects?
Quality gates in SAP automotive projects monitor key milestones like product design, production planning, and delivery.
- Example in SAP PP (Production Planning): A quality gate might ensure that BOMs (Bills of Materials) and routings are accurately configured before production starts.
- Purpose: To ensure product quality and compliance with regulatory standards.
Example: A final assembly gate ensures that all safety features are installed and functioning before vehicles are released.
10. What are quality gates in SAP DevOps?
Quality gates in SAP DevOps ensure automated workflows meet performance and compliance standards.
- Examples in SAP DevOps:
- Code Quality Gates: Require clean, efficient code before merging.
- Test Automation Gates: Validate that automated tests meet coverage requirements.
- Deployment Gates: Ensure no critical issues exist before releasing changes to production.
Example: In an SAP DevOps pipeline, a code quality gate might reject code that fails unit tests or violates coding standards, ensuring only reliable changes are deployed.
11. What are quality gates in Agile?
Quality Gates in Agile are checkpoints teams use to verify work meets predefined standards before progressing further. Unlike traditional phased approvals, Agile quality gates are lightweight and integrated into the workflow. Here’s how they work in practice:
Key Examples of Agile Quality Gates
1. Sprint Review Gate
- Is the increment fully tested?
- Does it meet the “Definition of Done”?
- Are acceptance criteria signed off?
2. Code Merge Gate
- Unit tests pass?
- Peer review completed?
- Code coverage ≥ 80%?
3. Release Readiness Gate
- Performance benchmarks met?
- Zero critical bugs open?
- User documentation updated?
12. What is the quality gate rule?
Quality gate rules are predefined criteria a team must meet to move work forward in a project. Think of them as checklists that ensure work meets agreed standards before progressing. They’re designed to prevent teams from advancing work that’s incomplete, unstable, or misaligned with goals.
How They Work
1. Predefined: Rules are set early (e.g., “All code must pass security scans”).
2. Non-negotiable: No exceptions—if criteria aren’t met, work pauses until fixed.
3. Team-owned: Rules are created collaboratively, not imposed externally.
Examples
1. Code Quality:
- Zero critical bugs in testing
- 90% test coverage
- Peer review completed
2. Design Approval:
- UX prototypes validated by users
- Architecture diagrams signed off
3. Release Readiness:
- Performance benchmarks met
- Documentation updated
Why They Matter
1. Stop problems early: Catch issues when they’re cheaper to fix.
2. Align expectations: Everyone knows the “done” standard upfront.
3. Reduce rework: Avoid backtracking later in the process.
In Agile, these rules are often automated (e.g., blocking code merges if tests fail) or baked into ceremonies like sprint reviews. They’re not about bureaucracy—they’re about protecting the team’s time and output quality.