SAP Articles
5 SAP Manufacturing Secrets Your Consultant Won't Tell You
Noel DCosta
- Last Update :
Companies in the Manufacturing Industry today face enormous pressure to digitalize. The shop floor looks nothing like it did twenty years ago. Machines talk to each other. Data flows from sensors to systems. Customers demand real-time visibility into production. And if you’re still using paper-based processes or disconnected legacy systems? You’re already behind.
I’ve seen manufacturing companies struggle with this digital transformation. One automotive parts supplier told me they had 17 different systems tracking various aspects of production. Nothing connected. Nothing synchronized. It was a nightmare.
This is where SAP comes in. But implementing SAP in manufacturing isn’t like implementing it in other industries. The statistics tell a concerning story. According to recent industry reports, manufacturing companies experience a 15% higher SAP implementation failure rate than other sectors.
About 30% of manufacturing SAP projects exceed their budget by more than 50%. And nearly 40% fail to deliver the expected business benefits.
Do you know why this is? Manufacturing has unique requirements that other industries don’t face. Complex routings. Multi-level bills of materials. Shop floor data collection. Quality control integration. Machine connectivity. The list goes on.
In this article, I’ll walk you through the specific challenges manufacturing companies face when implementing SAP. I’ll cover the essential modules for manufacturing. We’ll look at common pitfalls and how to avoid them.
I’ll share integration strategies for connecting SAP to your production environment. And most importantly, I’ll give you practical solutions that I’ve seen work in real manufacturing settings.
Let’s explore how to make your manufacturing SAP implementation successful.

Manufacturing success with SAP hinges on seamlessly integrating shop floor operations with your business processes, not just implementing software.The difference between struggling and thriving with SAP in manufacturing is proper master data management – your BOMs and routings must be accurate from day one.
The Manufacturing Industry Landscape Today

Digital Transformation in Motion
Let me tell you what’s really happening in manufacturing today. It’s changing constantly. Digital transformation isn’t some fancy term consultants throw around—it’s literally about survival now.
I was visiting a Steel Manufacturing factory in Dubai last month that honestly looked more like a technology company with some equipment thrown in. Remember when we all thought of manufacturing as just assembly lines and manual labor? Well, those days are pretty much over.
The whole Industry 4.0 thing has completely changed what manufacturers can do on their floors:
- Machines that can actually diagnose their own problems
- Sensors everywhere collecting data while production happens
- Maintenance systems that predict failures before they happen
- Virtual production simulations that test everything before building it
I was looking at a study recently that found about 67% of manufacturers are trying to digitally transform, but only about 24% feel they’ve really gotten there. The rest are stuck in this middle ground where they’ve got some new tech but are still dealing with their old systems too.
Manufacturing Complexity
Manufacturing is just plain complicated. There’s so much going on. Just think about what happens in a normal factory: you’ve got materials coming in, quality checks, inventory management, planning production, setting up machines, actual manufacturing, checking quality during production, packaging everything, managing the warehouse, and shipping products out. That’s a lot to handle! And each step creates data you need to track.
The thing is, if a retail store messes up, maybe a customer gets annoyed. If manufacturing messes up? You’ve got actual physical problems which includes wasted materials, products that need redoing, and shipments that don’t go out on time. The stakes are higher.
Regulatory Pressures
Then there’s all the regulatory stuff to deal with. Depending on what you make, you might need to comply with:
- FDA rules if you’re making medical stuff or pharmaceuticals
- ISO standards for your quality systems
- Special automotive requirements if you supply car parts
- Strict aerospace specs if you’re in that industry
- Environmental regulations that get stricter every year
And every single one of these requires tons of documentation and the ability to trace everything you do.
Competitive Landscape
The market isn’t making things any easier. Your customers want customized products, they want them faster, and oh yeah, they want them cheaper too. You’ve got competitors all over the world looking to take your business.
And then those supply chain messes of the last few years showed everyone how vulnerable their operations really are.
Why SAP Dominates Manufacturing
This is exactly why so many manufacturers turn to SAP. It gives you one system that connects everything. Your materials planning, production scheduling, quality management, warehouse operations, and financial tracking all work together instead of fighting each other. SAP is built to handle all these interconnected processes that you deal with every day.
The most important thing SAP gives you is visibility. When your customer calls asking where their order is, you need to tell them right now, not call them back in three hours after checking four different systems.
When something goes wrong on the production line, you need to figure out why immediately. These aren’t nice-to-haves anymore—they’re absolutely essential if you want to stay competitive.
The Manufacturing Industry Landscape and How SAP Addresses These Requirements
Manufacturing Requirement | Industry Challenge | SAP Solution/Capability |
---|---|---|
Production Planning | Balancing demand variability with finite resources across global plants. | SAP S/4HANA PP and SAP IBP for real-time planning, capacity checks, and simulations. |
Supply Chain Resilience | Disruption from geopolitical, raw material, or logistics instability. | SAP Digital Supply Chain (DSC) and SAP Business Network for supplier collaboration and visibility. |
Shop Floor Integration | Lack of real-time visibility into production execution and machine status. | SAP Digital Manufacturing Cloud (DMC) for execution, performance monitoring, and machine connectivity. |
Inventory Optimization | Excess stock tied up in working capital or frequent stockouts. | SAP Extended Warehouse Management (EWM) and SAP IBP inventory optimization capabilities. |
Product Quality Management | High defect rates, non-compliance, or late detection of process errors. | SAP S/4HANA QM for inspection, audit, and complaint processing integrated with production. |
Asset Maintenance | Unplanned equipment downtime affecting throughput. | SAP PM and SAP Asset Performance Management (APM) for preventive and predictive maintenance. |
Traceability & Compliance | Meeting regulatory standards for safety, batch tracking, and recalls. | SAP Global Batch Traceability and compliance content in SAP EHS and PP-PI. |
Make-to-Order / Configure-to-Order | Managing variant-rich products and dynamic BOMs. | SAP VC (Variant Configuration) and Advanced Available-to-Promise (aATP) in S/4HANA. |
Workforce Productivity | Lack of insight into labor efficiency and skill utilization. | SAP SuccessFactors integration with manufacturing KPIs and shop floor roles. |
Cost Management | Inaccurate product costing and lack of visibility into production variances. | SAP Product Costing and SAP Controlling (CO) integration with PP and MM modules. |
Related Topics: SAP Manufacturing & Production
Tailoring SAP for Factories
Key adjustments that make SAP fit discrete and process manufacturing lines.
Production Planning Essentials
Set up PP correctly so capacity, materials, and schedules stay in sync.
EWM Links to Production Flow
Understand how staging, picking, and goods receipt affect plant efficiency.
Clean Core in Manufacturing Projects
Reduce technical debt in your factory systems with clean SAP design principles.
Common SAP Modules for Manufacturing

You know what I hear all the time when talking to manufacturing folks about SAP? Total confusion about all those modules. So let me break down the ones you really need to understand for your manufacturing operation.
1. Production Planning (SAP PP)
This right here is the heart of manufacturing in SAP. It handles all your BOMs, work centers, routing, and production orders. Basically, it’s where you figure out what to make, when to make it, and how much to make.
I was working with this furniture company last year, and they cut their production planning time by 60% after getting this module right. What PP does really well is connect your sales forecasts to your actual production capacity, so you’re not making promises to customers that your shop floor can’t keep.
2. Materials Management (SAP MM)
MM keeps track of all your inventory, purchasing, and material movements. It’s watching your raw materials, work-in-process, and finished goods.
The best part about MM? It talks directly to Production Planning, so when production schedules something, it automatically triggers purchasing requirements. No more emergency runs to get materials or tying up all your cash in excess inventory.
3. Plant Maintenance (SAP PM)
Let’s be honest – equipment breakdowns are expensive as hell. The PM module helps you schedule preventive maintenance, manage repairs, and track equipment history.
One of my automotive clients cut their unplanned downtime by 35% in the first year after implementing PM. That’s serious money going straight to your bottom line.
4. Quality Management (SAP QM)
QM takes care of all your inspection processes, quality certificates, and defect tracking. You can create inspection plans tied to specific materials or processes and watch those results over time.
What makes QM so powerful is how it connects to other modules. Quality issues can automatically stop production orders, notify suppliers, or trigger maintenance requests.
5. Product Lifecycle Management (SAP PLM)
PLM manages your product data from start to finish – from when someone first sketches it on a napkin through design, manufacturing, service, and eventually retirement. If you make complex products or deal with lots of engineering changes, you need this.
PLM works with ECTR to handle your CAD integration, document management, change processes, and product structures. This is where your engineering team and production people finally start speaking the same language.
6. Production Planning for Process Industries (SAP PP-PI)
If you’re making stuff in batches like food, chemicals, or pharmaceuticals, you need PP-PI. It handles all those process manufacturing quirks like co-products, by-products, and batch management.
7. Manufacturing Execution (SAP MES)
MES is your connection to the actual shop floor. It manages production execution, labor tracking, and machine integration. This is where your operators interact with the system to report what’s happening in real-time.
Integration: Where The Real Magic Happens
Here’s what makes SAP so powerful for manufacturing: all these modules actually work together. When PP creates a production order, MM automatically reserves materials.
When QM finds a problem, it can stop that production order from moving forward. When PM schedules maintenance, PP adjusts your capacity planning.
This integration is what breaks down those departmental silos that are killing your efficiency. You get one version of the truth across your whole operation, and everybody’s finally on the same page.
Integration Requirements in Manufacturing Industry and How SAP Addresses This Requirement
Integration Requirement | Industry Need | SAP Capability |
---|---|---|
ERP–MES Integration | Seamless data exchange between planning systems and shop floor execution. | SAP Digital Manufacturing integrates with SAP S/4HANA for real-time order and material tracking. |
SCADA / PLC Integration | Machine-level connectivity to trigger alerts, status updates, and energy data. | SAP Plant Connectivity (PCo) connects SCADA/PLC to SAP systems using standard protocols (OPC, MQTT). |
Supply Chain Integration | Visibility into supplier capacity, ASN, and logistics execution. | SAP Business Network and Integration Suite support end-to-end supply chain collaboration. |
Warehouse Integration | Live updates between warehouse systems and production orders. | SAP EWM and SAP Manufacturing Integration & Intelligence (MII) synchronize inventory and production flows. |
Quality Management System (QMS) | Exchange inspection results, alerts, and deviations between QMS and ERP. | SAP S/4HANA QM integrated with production and logistics for real-time inspection feedback. |
CAD/PLM Integration | Transfer engineering BOMs and changes into production systems efficiently. | SAP Engineering Control Center (ECTR) integrates CAD systems directly with SAP PLM and S/4HANA BOMs. |
Third-Party Equipment Systems | Integrate legacy machines and proprietary software with enterprise systems. | SAP PCo and SAP MII provide adapters and scripting engines for custom system integration. |
Cloud-to-Edge Integration | Enable sensor data, IoT events, and real-time telemetry from factory floor to cloud. | SAP Edge Services and SAP BTP IoT integrate field data into central SAP analytics and DMC. |
HR and Shop Floor Systems | Link labor data, shift plans, and training records to manufacturing execution. | SAP SuccessFactors integrates with DMC and MES for skill-based resource allocation. |
Analytics & BI Integration | Combine manufacturing KPIs from ERP, MES, and sensors for decision support. | SAP Analytics Cloud and SAP Data Warehouse Cloud offer cross-layer reporting and visualization. |
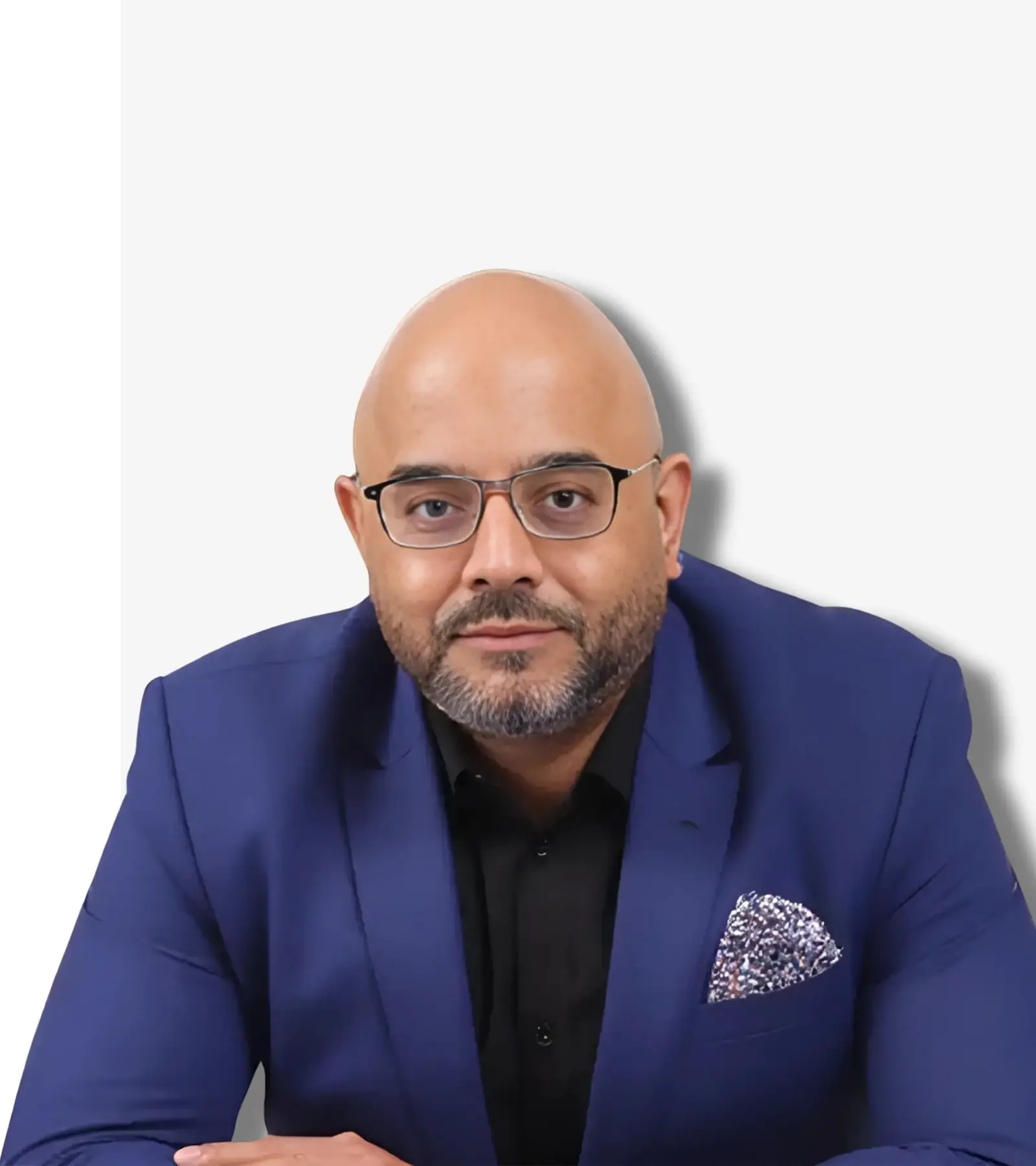
See How I Make Your ERP and AI System Selection or Implementation right for you.
ERP & AI System Selection – Identify and choose the right ERP or AI-enabled platform to fit your business needs.
Project Support & Recovery – Keep your project on track or bring failing implementations back under control.
ERP Modernization – Transform existing ERP systems to modern, efficient, and scalable ERP environments.
GET IN TOUCHTop Implementation Challenges in the Manufacturing Industry

I want to share the real challenges I’ve seen manufacturers struggle with during SAP implementations. These aren’t just theoretical problems – they’re the actual headaches that wake up project managers at 3 AM in a cold sweat.
1. Complex Production Processes and Routing
You know how manufacturing processes almost never follow a nice, simple path? Well, that creates huge challenges in SAP. Think about your own processes – you probably have parallel operations, multiple possible routings, rework loops, and conditional steps. Getting all this configured in SAP is seriously difficult.
I remember a metal fabrication company that had more than 200 routing combinations for just one product family.
They thought mapping these into SAP would take 6 weeks. It took 12. And the real problem wasn’t just setting it up – it was testing everything to make sure it worked in all situations.
2. Bill of Materials (BOM) Complexity
Let’s talk about your BOMs for a minute. In manufacturing, these can get incredibly complicated:
- Multi-level structures going 10+ levels deep
- Hundreds of components per finished product
- Alternative materials that can be substituted
- Quantities that change based on batch size
- Revision management that tracks changes over time
I had a client in electronics manufacturing with BOMs containing 15 levels of components. Each component had engineering change history they needed to preserve. The data migration alone nearly derailed their whole project.
3. Shop Floor Integration Issues
One of the toughest parts? Getting SAP to talk to your actual machines on the floor. Your equipment, barcode scanners, RFID systems, and quality testing tools all need to connect with SAP.
The truth is that these connections usually need custom development. If your implementation team doesn’t have specialized experience with shop floor integration, you’re going to hit major roadblocks.
4. Legacy System Replacement Hurdles
You’re probably not starting with a blank slate. You’ve got existing systems with years (maybe decades) of data. So you need to figure out what to bring over, how to transform it, and when to make the switch.
The hardest part is deciding what historical data you really need. I’ve watched management teams debate this for weeks. This gets even trickier if you’re in a regulated industry where you might need to keep manufacturing records for compliance reasons.
5. Master Data Management Complexities
Here’s something I tell all my clients: your master data will make or break your implementation. Materials, BOMs, routings, work centers – all this needs to be clean and consistent.
I can’t stress this enough. I saw an automotive supplier discover they had the same exact parts defined five different ways across their plants. They had to delay their go-live by three months just to sort out the mess.
6. Reporting and Analytics Requirements
Your manufacturing operation generates tons of data. The challenge is turning that into useful information.
You need production metrics, quality stats, equipment effectiveness measures, and cost breakdowns. Setting these up means understanding both what the business needs to see and where exactly that data lives in SAP.
7. Change Management for Shop Floor Personnel
But you know what? The biggest challenge usually isn’t technical at all – it’s people. Your shop floor workers might have been doing things the same way for 15 years. Now you’re asking them to use tablets, scan barcodes, and enter data while they work.
I’ve seen technically perfect implementations crash and burn because the people actually doing the work weren’t properly trained or motivated.
This needs special attention in manufacturing where your workforce might not be as comfortable with technology as other departments.
Your SAP manufacturing implementation will only be as strong as your weakest integration point, which is typically where your production equipment meets your digital systems.
Data Migration Considerations in the Manufacturing Industry

Data migration is where many manufacturing SAP implementations hit a wall. Let me share what I’ve learned from helping dozens of manufacturers through this process.
1. Production Data Migration Complexities
Your production data is among the most complex to migrate. You’ve got work orders in various stages of completion, labor hours already applied, and materials already consumed. Deciding how to handle these in-flight processes is tough.
I usually recommend setting a clear cutoff date. Complete as many work orders as possible in the legacy system before that date. For orders that must transfer mid-process, you’ll need detailed mapping to preserve their status and history.
2. BOM and Routing Data Transition
Your Bills of Materials and routings are the backbone of your manufacturing operations. Getting these right in SAP is absolutely critical.
The challenge here isn’t just moving the data—it’s restructuring it to fit SAP’s framework. Your legacy system probably has different levels of detail and different relationships between components. You’ll need to harmonize naming conventions and carefully validate each BOM after migration.
3. Historical Quality Data Preservation
If you’re in a regulated industry, you may need to keep years of quality data available. Even if you’re not, this historical information has tremendous value for analysis.
You have options here:
- Migrate all historical data (expensive but complete)
- Migrate summary data only (more manageable but loses detail)
- Keep the legacy system available in read-only mode (avoids migration but requires maintaining two systems)
The right approach depends on your regulatory requirements and how you use historical quality data.
4. Inventory and Material Master Challenges
Your material master data drives everything in SAP. Inconsistent units of measure, duplicate items, and missing attributes will cause headaches throughout your implementation.
Start cleaning this data early—months before your actual migration. Focus on standardizing descriptions, units of measure, and classification systems. Dedicate business resources who really understand the materials to validate the data.
5. Data Cleansing for Manufacturing-Specific Records
Manufacturing data has unique challenges. Work center availability, machine capacities, setup times, and resource requirements all need careful cleansing.
I’ve found that involving production supervisors in this cleansing process is essential. They know the real capacities and limitations of their equipment, often better than what’s documented.
6. Testing Strategies for Production Data
Test your migrated data thoroughly in a realistic environment. Create test production orders, run MRP, and simulate your manufacturing processes end-to-end.
Don’t just check record counts—validate that the business processes work correctly with your migrated data. This rigorous testing will catch issues before they impact your actual operations.
Proposed SAP Implementation Solution Approaches for the Manufacturing Industry
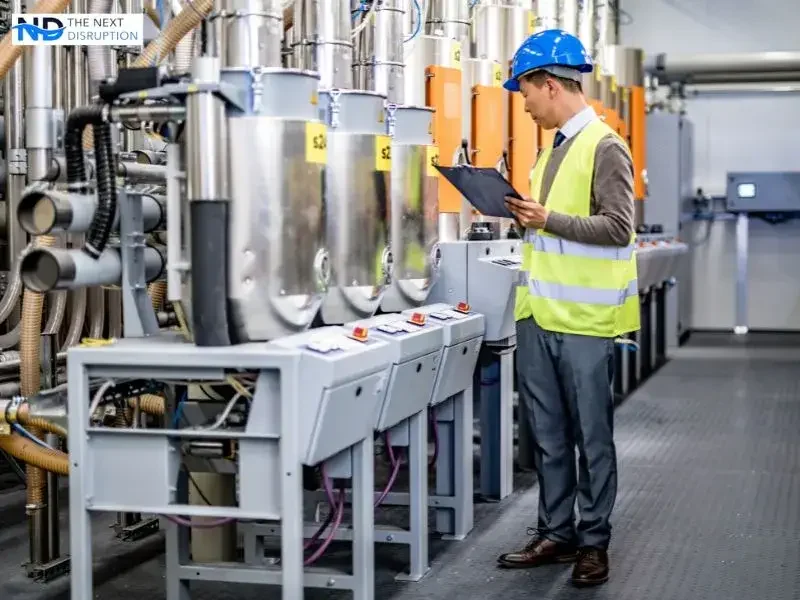
So how do you tackle these SAP implementation challenges in manufacturing? Let me share some approaches that I’ve seen work well in the real world.
Phased vs. Big-Bang Implementation Strategies
You’ve got two main options here. Big-bang means switching everything to SAP at once. Phased means implementing module by module or plant by plant.
Most of the manufacturing companies I work with end up choosing a phased approach. It reduces risk and allows your team to learn from each phase.
One auto parts client implemented SAP in their smallest plant first, worked out the kinks, then rolled it out to larger facilities. This saved them from repeating the same mistakes at scale.
That said, big-bang can work if you have strong project management, adequate resources, and clear executive support. Just be realistic about the challenges.
Templated Approaches for Manufacturing
Don’t reinvent the wheel. SAP offers industry-specific templates for manufacturing that incorporate proven configurations.
I’ve seen companies cut their implementation time by 30-40% using these templates. They give you a solid starting point that you can then adapt to your specific needs. Think of them as a head start rather than a complete solution.
Industry Best Practices Adoption
This is a huge opportunity many manufacturers miss. SAP contains built-in best practices developed from thousands of implementations worldwide.
When you’re configuring SAP, resist the urge to replicate your existing processes exactly. Instead, ask “why do we do it this way?” and consider adopting SAP’s recommended approaches. One electronics manufacturer I worked with eliminated 12 unnecessary approval steps by simply adopting standard processes.
Shop Floor Integration Strategies
Connecting SAP to your production equipment requires specialized approaches. You’ve got several options:
- Direct integration using SAP Manufacturing Integration and Intelligence (MII)
- Middleware solutions that translate between machine protocols and SAP
- Third-party Manufacturing Execution Systems (MES) that bridge the gap
The best choice depends on your equipment, budget, and requirements. Whatever you choose, bring your IT and OT (operational technology) teams together early to plan this integration.
Mobile Solutions for Plant Workers
Your shop floor workers need simple, accessible ways to interact with SAP. Mobile solutions on tablets or ruggedized devices can dramatically improve adoption.
Focus on creating intuitive interfaces that require minimal training. One food manufacturer equipped their line workers with tablets running simplified SAP transactions. They saw data entry errors drop by 65% compared to their previous paper-based system.
Customization vs. Standard Functionality Decisions
Here’s my advice after seeing dozens of implementations: customize only where it delivers clear competitive advantage. Otherwise, adapt your processes to SAP standards.
Every customization adds complexity, cost, and upgrade challenges. Before approving any customization, ask if it’s truly necessary for your business success or just preserving “the way we’ve always done it.”
Related Topics: SAP in Manufacturing Operations
S/4HANA for Manufacturing
Explore how S/4HANA supports MRP, quality, and supply chain integration in real-time.
Connect Machines and SAP
Use the right SAP integration tools to bridge shop floor systems with ERP.
Cost Control with SAP FICO
Track actual vs. planned production costs with proper SAP FICO setup.
EHS Management in Plants
Use SAP EHS to track incidents, audits, and safety KPIs across facilities.
Technology Integration Points for an SAP Manufacturing Implementation

Getting SAP to talk to your other manufacturing systems isn’t just a technical challenge – it’s essential for realizing the full value of your implementation. Here’s what you need to know about the key integration points.
MES System Integration
Your Manufacturing Execution System (MES) bridges the gap between SAP and your shop floor. This integration is critical for accurate production reporting and scheduling.
I worked with a medical device manufacturer who struggled for months with duplicate data entry between their MES and SAP. Once we established proper integration, they saved 20+ hours of admin work weekly and dramatically improved data accuracy. The key is establishing clear “system of record” rules for which system owns which data.
IoT and Sensor Data Incorporation
Your machines are generating valuable data every second. Temperature readings, pressure levels, cycle times – all this can flow into SAP to improve decision-making.
SAP’s IoT capabilities allow you to set up automated alerts, trigger maintenance orders, and track actual vs. expected performance.
One chemical producer I worked with connected their reactor sensors directly to SAP, enabling real-time quality adjustments that reduced off-spec product by 23%.
Barcode/RFID Scanning Solutions
Manual data entry is the enemy of accuracy. Barcode and RFID scanning eliminates this problem while speeding up processes.
The most successful implementations I’ve seen integrate scanning at every key point: material receipt, production consumption, labor tracking, and shipping. Your workers will resist at first, but once they experience how much easier it makes data recording, they’ll never want to go back.
Automated Quality Testing Equipment Integration
If your quality testing equipment isn’t connected to SAP, you’re missing a huge opportunity. Direct integration ensures test results are captured accurately and immediately.
This integration can trigger automatic holds on non-conforming materials, update quality certificates, and track statistical process control metrics. The result is faster release of good product and better containment of quality issues.
Third-party Specialized Manufacturing Applications
Most manufacturers use specialized applications beyond SAP – statistical process control, recipe management, formulation systems, or specialized scheduling tools.
Rather than replacing these, focus on clean integration points. Define clear data flows, ownership boundaries, and synchronization procedures.
Real-time Data Collection Considerations
Real-time data is powerful but comes with challenges. Network reliability, data volume, and processing capacity all need careful planning.
Start by identifying what truly needs to be real-time versus what can be batch-processed. Production counts and quality holds might need immediate updates, while detailed labor reporting could be batched hourly or by shift.
Technology Integration Points for an SAP Manufacturing Implementation
Integration Point | Technology Layer | SAP Component or Tool |
---|---|---|
ERP ↔ MES | Application Integration | SAP Digital Manufacturing Integration with SAP S/4HANA (production order sync, confirmations) |
Shop Floor ↔ Machine Layer | Operational Technology (OT) | SAP Plant Connectivity (PCo) and SAP Edge Services |
SCADA/PLC ↔ SAP Systems | Machine Integration | SAP PCo with OPC UA, MQTT, REST adapters |
Quality System ↔ Manufacturing | Process Control Layer | SAP S/4HANA QM and integration with SAP DMC |
Warehouse ↔ Production Execution | Execution Integration | SAP EWM integrated with S/4HANA PP or DMC |
PLM/CAD ↔ ERP/MES | Engineering Integration | SAP Engineering Control Center (ECTR), SAP PLM |
Sensor/IoT ↔ Analytics | IoT/Streaming Layer | SAP BTP IoT Services, SAP Edge Integration, Event Mesh |
ERP ↔ HR and Scheduling | Business Integration | SAP SuccessFactors, integration with DMC for labor modeling |
ERP ↔ External Suppliers | Network Integration | SAP Business Network (Ariba, Logistics Business Network) |
Analytics ↔ Operational Systems | Data & Analytics Layer | SAP Analytics Cloud, SAP Data Warehouse Cloud, embedded analytics |
SAP ECTR: Streamlining Engineering and Manufacturing Integration
Let me tell you about one of the most underrated tools in the SAP manufacturing world – ECTR. If you’ve ever dealt with the frustrating disconnect between your engineering team and production floor, you’re going to want to pay attention to this.
What is SAP ECTR?
SAP ECTR (Engineering Control Center) is basically the missing link between your CAD systems and your SAP environment. I’ve seen so many manufacturers where engineering does their thing in one system while production works in SAP, and the two barely talk to each other. It’s like they’re speaking different languages.
What ECTR does is create that bridge. All your engineering data – your CAD models, drawings, specs, BOMs – flows directly into SAP without someone having to manually reenter everything.
When engineering makes a design change, your manufacturing data updates automatically. No more working from outdated information.
Key Benefits for Manufacturers
I’ve watched ECTR completely change how companies operate. Here’s what you can expect:
- No more manual copying of data between systems (and all the errors that come with it)
- Design changes automatically sync with production data
- Change management processes that used to take weeks now happen in days
- Your production team gets immediate access to the latest designs
- Better traceability for compliance and quality management
I recently worked with an automotive parts company that was spending about three weeks implementing each engineering change. After ECTR? They got it down to just 5 days. That’s a huge competitive advantage when you need to make product improvements quickly.
Implementation Considerations
If you’re thinking about ECTR, here are some things to keep in mind:
- Check if your CAD system plays nice with ECTR (most major ones do)
- Look at your current engineering change process – it will need some adjustments
- You’ll probably need to clean up some data before integration
- Both your engineering and production people will need training
I’m not going to lie to you – implementing ECTR isn’t a walk in the park. But for manufacturers dealing with frequent design changes or complex products, it’s becoming essential. The time and error reduction alone usually justify the investment.
What’s your experience with engineering and production integration? Have you tried ECTR or similar solutions?
Case Study Examples for the Manufacturing Industry

Let me share some real-world stories from SAP implementations I’ve been involved with. These examples illustrate both successes and challenges you might face in your own manufacturing environment.
1. Precision Engineering Success Story
A precision engineering company that makes aircraft components implemented SAP across their five plants. Their previous system couldn’t handle their complex routings and quality requirements.
Their smart approach? They started with master data cleanup six months before implementation. They assigned dedicated business experts to standardize part numbers, BOMs, and work centers across all plants. This upfront investment paid off enormously during implementation.
They also made a tough but important decision to adopt SAP standard processes rather than customizing to match their existing workflows. This required retraining staff, but ultimately gave them access to better functionality and easier upgrades.
The results were impressive. They reduced inventory by 22% while maintaining the same service levels. Production scheduling time decreased from three days to four hours. And most importantly, they achieved full traceability for their aerospace customers, opening up new business opportunities.
2. Chemical Manufacturing Learnings
A specialty chemicals manufacturer took a different approach that revealed important lessons. They insisted on heavily customizing SAP to match their existing processes, creating over 200 custom reports and modifications.
The implementation took 8 months longer than planned and went 40% over budget. When they finally went live, the custom elements caused numerous integration problems. Even worse, these customizations made their first upgrade project a nightmare.
Their key learning? They should have spent more time understanding SAP’s standard capabilities before deciding to customize.
Many of their “unique” processes weren’t actually providing competitive advantage – they were just familiar ways of working.
Common Pitfall: Underestimating Shop Floor Adoption
One automotive supplier did everything right technically but failed to adequately prepare their shop floor workers. They invested millions in a perfectly configured system, only to have production workers resist using it.
The implementation team had focused on management reporting needs while neglecting the user experience for machine operators. The complicated interfaces and numerous required fields made daily work more difficult.
Their solution was to bring shop floor workers into the project, redesign the interfaces with user input, and develop better training programs. This delayed their full implementation by months but ultimately saved the project.
Implementation Timeline and Resources
So you’re wondering how long this SAP thing is really going to take and what kind of people you’ll need to pull it off? Let me share what I’ve learned from being in the trenches with manufacturing companies just like yours.
Realistic Implementation Timeline
I’m not going to sugarcoat this. For a typical mid-sized manufacturer, you should plan on 12-18 months from kickoff to actually going live. Could it be done faster? Maybe, but I’ve honestly never seen it happen without creating bigger problems down the road.
Here’s roughly how the timeline usually breaks down:
- Getting organized and planning: 1-2 months
- Figuring out your processes and requirements: 2-3 months
- Setting up and developing the system: 3-4 months
- Making sure everything works together: 2-3 months
- Training your people and final testing: 2-3 months
- Moving your data and switching over: 1-2 months
One thing I always tell my clients: whatever timeline seems reasonable to you right now? Add 20% more time. Trust me on this one. Manufacturing implementations always hit unexpected complications that throw off your schedule.
Manufacturing-Specific Resource Needs
You need people who understand both SAP and how manufacturing actually works. And let me tell you, that combination isn’t easy to find.
Your team should definitely include:
- Supervisors who deal with production headaches every day
- Engineers who understand your manufacturing processes
- Quality people who know your testing requirements
- Actual shop floor workers who can tell you when an idea won’t work
- IT folks who know your equipment and systems
Here’s a tip most consultants won’t tell you: about 40% of your team should come from operations, not just IT or finance. If your team is all tech people and accountants, your implementation won’t address the real needs on your factory floor.
Budgeting Realities
I hate to be the bearer of bad news, but manufacturing implementations almost always cost more than SAP projects in other industries. All those connections to production equipment, specialized manufacturing modules, and complex testing requirements add up fast.
From what I’ve seen, manufacturing companies typically end up spending somewhere between 1-3% of their annual revenue on their SAP implementation.
Where you fall in that range depends on your size, complexity, and how many locations you have.
And don’t forget to budget for all that shop floor hardware – scanners, tablets that can survive in a factory environment, label printers, and network equipment. These costs sneak up on you if you’re not careful.
Key Roles For Success
Beyond the usual SAP project roles, you need some manufacturing specialists:
- Someone who can translate your production requirements into SAP configuration
- A technical person who knows how to connect SAP to your actual machines
- A data migration expert who understands complex BOMs and routings
- Someone focused on helping your production staff adapt to the new system
These manufacturing-specific roles often get overlooked, but they’re absolutely critical to your success. Without them, you’ll end up with a system that works great for accounting but falls apart on the shop floor.
Post-Implementation Considerations
So you’ve finally gone live with SAP. Pop the champagne! But wait… the journey isn’t over. Actually, this is where the real work begins. Let me share what happens after the consultants pack up their laptops and head out.
Ongoing Support Needs
Here’s something most vendors won’t tell you. Your manufacturing operations run around the clock, and your SAP support needs to do the same. Your system doesn’t care if it’s 2 AM when it decides to have problems.
I remember a food manufacturer who thought their regular IT helpdesk could handle SAP issues. They learned the hard way that wasn’t going to work.
When they had a production order crisis in the middle of the night, there was nobody who could fix it. Production literally stopped for hours.
You need specialized support for:
- Production order problems
- Material availability issues
- Quality holds and releases
- Shop floor transaction errors
If your team can’t handle this 24/7, you might need to look at external support options. It’s worth every penny when you’re staring at a stopped production line.
Continuous Improvement Strategies
The SAP system you go live with on day one should absolutely not be the same system you have a year later. If it is, you’re doing something wrong.
Your processes will keep evolving, and your system needs to keep up. Set up a way for your production teams to submit ideas for improvements. Then actually implement the ones that will make the biggest difference.
I’ve seen this work incredibly well. One chemical company collected improvement ideas directly from their operators and implemented the best ones every quarter.
The operators loved seeing their ideas come to life, and the company got substantial efficiency improvements.
Training Requirements for Manufacturing Personnel
Let’s be real about training. Your shop floor staff will need ongoing education – not just a one-time crash course during implementation.
People forget stuff. Processes change. New employees come on board. You need to keep the knowledge fresh with:
- Simple guides for everyday transactions
- Short videos showing complex processes
- Refresh sessions every few months
- Programs where experienced users teach others
Measuring ROI in Manufacturing Environments
How do you know if all this SAP investment was actually worth it? You need to track the right metrics.
Don’t just look at general financial numbers. You need manufacturing-specific indicators like:
- How much you’ve cut production planning time
- Whether on-time deliveries have improved
- If quality holds have decreased
- How much inventory levels have dropped
- Whether machine utilization has increased
I worked with an automotive supplier who found their entire SAP implementation paid for itself in just 14 months.
The big wins came from inventory reduction and better production scheduling. But they only knew this because they were smart enough to measure these things from the beginning.
Remember, what gets measured gets improved. Make sure you’re tracking the metrics that actually matter to your manufacturing operation.
Related Topics: SAP for Manufacturing Teams
Production Planning with SAP PP
Learn how SAP PP helps you plan, execute, and track production orders with accuracy.
SAP EWM for Manufacturers
Streamline warehouse operations and improve stock accuracy with SAP EWM.
Clean Core Strategy for Plants
Understand how clean core principles reduce custom code in manufacturing processes.
Manufacturing Analytics in SAP
Use SAP Analytics Cloud to monitor KPIs across production, inventory, and logistics.
Conclusion

Wow, we’ve covered a ton of ground here about SAP implementation in manufacturing. From those really complex BOMs to all the shop floor integration stuff, from data migration nightmares to getting your people on board – this isn’t an easy journey, but I promise it’s worth the effort when done right.
So what’s next for SAP in manufacturing? Well, everything is moving toward cloud solutions, smarter analytics with AI, and connecting more directly with your production equipment. Manufacturing is changing fast, and your systems need to keep up or you’ll be left behind.
If you’re thinking about jumping into an SAP implementation for your factory, here’s my honest advice: start by understanding what your business actually needs, not what the technology can do.
Be super realistic about how long it will take and who you’ll need on your team. And please, put your manufacturing folks at the center of everything – they’re the ones who will make or break your success.
Hey, I want to hear from you! Have you gone through a manufacturing SAP implementation? What surprised you the most? What clever solutions did you come up with? Drop a comment below and share your story.
Your experience might save someone else from making the same mistakes or help them find a better path forward. We’re all in this together!
Additional Resources
Listen, you don’t have to figure all this SAP manufacturing stuff out by yourself. There are tons of resources that can make your life easier. I’ve personally found these to be super helpful during tough implementations.
If you’re looking to connect with other people facing the same challenges, check out these user groups:
- ASUG (Americas’ SAP Users’ Group) has a really active manufacturing community
- SAP Manufacturing Industry Forum where people share what’s working and what isn’t
- Local SAP User Groups often have manufacturing subgroups where you can meet people in your area
Need ongoing support and ideas? I regularly use these resources:
- The Manufacturing forums on SAP Community Network – real users sharing real solutions
- ManEx conferences – great for networking with other manufacturing SAP users
- LinkedIn groups focused on SAP Manufacturing – just filter out the sales pitches
SAP does provide good documentation for manufacturing, but it can be hard to find what you need. The Manufacturing section of the SAP Help Portal is worth bookmarking, though it won’t always give you the practical answers you’re looking for.
Here’s my biggest tip for choosing consultants: don’t just look at their SAP certifications. I’ve seen “certified experts” who’ve never set foot in a factory. Ask for manufacturing-specific case studies. Check their references thoroughly.
And do this – bring potential consultants to your shop floor and watch how they interact with your production staff. You’ll know within 15 minutes if they truly understand manufacturing or if they’re just tech people who talk a good game.
What other resources have you found helpful? Share in the comments below!
If you have any questions, or want to discuss a situation you have in your SAP Implementation, please don't hesitate to reach out!
Questions You Might Have...
1. What do you mean by manufacturing?
Manufacturing is the process of converting raw materials into finished products through various operations like machining, forming, joining, and assembly. It involves transforming inputs into outputs with added value.
2. What is known as manufacturing?
Manufacturing is known as the industrial production process where raw materials are transformed into finished goods on a large scale using machinery, tools, chemical processing, and labor.
3. What is the meaning of manufacturing business?
A manufacturing business is a company that produces physical products by converting raw materials into finished goods. These businesses typically operate factories or production facilities and sell their products to distributors, retailers, or directly to consumers.
4. What is SAP for manufacturing?
SAP for manufacturing is a suite of integrated software modules specifically designed to manage manufacturing operations. It handles production planning, execution, quality management, maintenance, inventory, and financial aspects of manufacturing businesses.
5. What are the types of manufacturing in SAP?
SAP supports several types of manufacturing:
- Discrete manufacturing (individual products)
- Process manufacturing (batches and formulations)
- Repetitive manufacturing (high-volume production lines)
- Make-to-order manufacturing
- Engineer-to-order manufacturing
- Mixed-mode manufacturing (combination of types)
6. What is SAP process manufacturing?
SAP process manufacturing is a specialized set of functionality in SAP designed for industries that produce goods in batches using formulas or recipes (like food, beverages, chemicals, or pharmaceuticals). It handles batch management, formulations, co-products, by-products, and other process industry requirements.
7. What are SAP manufacturing modules?
The main SAP manufacturing modules include:
- Production Planning (PP)
- Materials Management (MM)
- Plant Maintenance (PM)
- Quality Management (QM)
- Manufacturing Execution (ME)
- Production Planning for Process Industries (PP-PI)
- Product Lifecycle Management (PLM)
8. What is ERP in manufacturing?
ERP (Enterprise Resource Planning) in manufacturing is a comprehensive software system that integrates all aspects of manufacturing operations including production, inventory, purchasing, sales, finance, and human resources. It provides a single source of truth for all business data and processes.
9. How to use SAP for production?
To use SAP for production, you typically create production orders based on demand, release these orders to the shop floor, issue materials, confirm production activities, report goods completion, and settle production costs. The specific steps vary based on your manufacturing approach and configuration.
10. What is MRP in SAP?
MRP (Material Requirements Planning) in SAP is a planning system that calculates material needs based on demand (sales orders, forecasts) and suggests purchase or production orders. It ensures you have the right materials at the right time while optimizing inventory levels.
11. What are the 4 levels of manufacturing?
The 4 levels of manufacturing typically refer to:
- Strategic level (long-term planning)
- Tactical level (medium-term planning)
- Operational level (short-term execution)
- Shop floor level (real-time execution)
In SAP terms, this might equate to strategic planning, MPS (Master Production Scheduling), MRP (Material Requirements Planning), and shop floor control.
12. What are factory methods in SAP?
Factory methods in SAP refer to the production strategies or approaches configured in the system. These include make-to-stock, make-to-order, assemble-to-order, engineer-to-order, and others. Each method has different planning, execution, and costing approaches in SAP.
13. What is BOM in SAP MM?
BOM (Bill of Materials) in SAP is a structured list of all components, raw materials, and sub-assemblies needed to produce a finished product. While BOMs are primarily managed in the PP (Production Planning) module, they interact with MM (Materials Management) for inventory management and procurement of the required components.
14. How to use SAP for production?
To use SAP for production, you typically create production orders based on demand, release these orders to the shop floor, issue materials, confirm production activities, report goods completion, and settle production costs. The specific steps vary based on your manufacturing approach and configuration.
15. What is the SAP module for manufacturing?
The primary SAP module for manufacturing is PP (Production Planning). This module handles production planning, capacity planning, material requirements planning, and production order management. Other key modules for manufacturing include MM (Materials Management), PM (Plant Maintenance), QM (Quality Management), and PP-PI (Production Planning for Process Industries).
16. What are the types of manufacturing in SAP?
SAP supports several types of manufacturing:
- Discrete manufacturing (individual products)
- Process manufacturing (batches and formulations)
- Repetitive manufacturing (high-volume production lines)
- Make-to-order manufacturing
- Engineer-to-order manufacturing
- Mixed-mode manufacturing (combination of types)
- Just-in-time manufacturing
- Lean manufacturing