SAP Modules
SAP Enterprise Warehouse Management (SAP EWM) Essentials
Noel DCosta
- Last Update :
Warehousing always looks straightforward from a distance. I used to think the same. But once you step into it, everything feels more reactive than planned. SAP EWM comes up a lot in conversations about fixing this. And, to be honest, it deserves that attention. There is no perfect system, sure, but this one has depth. SAP EWM lets you rethink how the entire space functions, not just individual tasks.
I have walked through warehouses that looked fine at first glance. Then I asked about their order cycle times. Or how often they had to re-slot inventory just to stay afloat. The answers felt uncertain. Some even shrugged. That is the real cost, uncertainty.
Most warehouse issues are not system related. They are systemic.
Not being able to locate a pallet is rarely just about that pallet. It usually points to something else:
Inefficient layout choices no one challenged
Manual processes left untouched for years
Systems that technically “work,” but never actually help
Sometimes, the tools people use are part of the problem. You log in, you check a number, but you cannot trust it. That erodes decisions over time. Slowly, but definitely.
The need for clarity is growing faster than operations can keep up.
Every business says they want visibility. But many still rely on spreadsheets to patch gaps their current systems cannot close. That feels risky now, especially with shorter order windows and higher customer expectations.
You might feel pressure to automate. Everyone talks about robotics and smart forklifts. That is fine. But none of it works unless the foundation holds. SAP EWM gives you that baseline i.e. inventory that reflects reality, processes that adapt under strain, and flexibility without rewriting everything.
So maybe the software is not magic. But when it is set up right, it makes a real difference. And that might be enough to matter.
What is SAP Enterprise Warehouse Management (SAP EWM)?

SAP EWM gives you more control over your warehouse, real control, not just numbers on a screen. If you manage floor operations or supervise shift changes, then you already know how quickly things go sideways when systems lag or teams lose track. SAP EWM helps tighten that up.
I have spoken to supervisors who said their old system was fine, until volume picked up or returns doubled. That is when problems start. Stock gets miscounted. Tasks pile up. People start working around the system instead of with it. SAP EWM gives you a way to stop chasing problems and start preventing them.
Things go wrong for reasons you can’t always see.
Someone misses a pick. A trailer backs in late. A cycle count shows a gap no one can explain. You know what that does, it slows the shift, shifts the next one, and eventually throws off your week. SAP EWM cannot stop trucks from arriving late, but it can show you where the delays begin and help you deal with them before they stack up.
It is not about replacing your team or overhauling your process. It is about seeing what is really happening and making better calls faster. Maybe that means rerouting a task. Maybe it means flagging a bin early. You stay ahead, and people stop getting blindsided.
What You Get with SAP EWM which is important
Real-time inventory control you can actually trust
Task visibility that follows each step, not just orders
Automation support when you are ready, not before
You probably manage things well already. But when the pressure builds, a better system like SAP EWM takes some of that weight off your shoulders. And that is worth looking at now.
SAP EWM depends heavily on accurate inventory master data. Even the most precise configuration breaks down when units of measure, pack sizes, or product dimensions are off.
I have seen simple errors like mismatched dimensions cause ripple effects across receiving and picking. The system only performs well when the foundation, your data, is clean and dependable.
10 Key Takeaways about SAP EWM
- SAP EWM is much stronger than the basic WM module in older SAP systems. It handles complex warehouse operations that basic WM just can’t manage.
- The system uses real-time data. Your inventory updates immediately when movements happen, not in batch jobs later. This gives you accurate stock visibility.
- Most companies see productivity gains of 15-25% in year one. Warehouse staff spend less time searching for items and more time moving them.
- Implementation takes 8-12 months for a single warehouse. Don’t trust anyone promising faster timelines without proper testing.
- The RF scanning integration cuts errors dramatically. Error rates typically drop by 80% compared to paper-based processes.
- EWM supports better slotting strategies. You can optimize bin locations based on how fast products move. This cuts travel time for pickers.
- The labor management functions track productivity. You establish standard times for warehouse work and see who’s hitting targets and who needs help.
- Integration with SAP TM creates huge value. Your warehouse operations sync with inbound and outbound shipments.
- The yard management tracks trailers on your property. No more lost trailers sitting in the yard for days.
- The system grows with you. Start basic and add voice picking, automation integration, or wave management as needed.
ROI Calculator: Estimate EWM Impact in 2 Minutes
Estimate EWM Impact in 2 Minutes
Use this quick tool to estimate the potential ROI from implementing SAP EWM in your warehouse. Just answer a few short questions.
Inside SAP EWM: The Core Components That Drive Success

SAP EWM is not just one thing. It is a system with a lot of moving parts. Each one does something important, but what really makes it work is how they all talk to each other. That connection is what keeps the warehouse running smooth when things start to get hectic.
I have used SAP EWM in a few different environments. And every time, it takes a little effort to set up, but once it is working, the difference is clear. Let me walk you through what actually matters.
1. Warehouse Structure Management
This is the part that lays the foundation. SAP EWM lets you build your warehouse in the system just like it looks in real life. Every storage bin, zone, and staging area gets defined so nothing is left floating.
I worked with a site that had over 45,000 bin locations. Before EWM, finding anything was half guesswork. After mapping everything, things got easier. Picking paths improved. And people stopped asking, “Where is this supposed to go?”
2. Inbound Processing
The system handles what comes in, right from the yard check-in through to putaway. It already knows what to expect, so as soon as the truck backs in, it guides the team through unloading, inspection, and storage.
At a food DC, I saw receiving time drop by nearly a third. They did not speed up the team. They just stopped making them figure out where to put stuff. The system told them. That was it.
3. Outbound Processing
Honestly, this is where SAP EWM pulls ahead. Once orders come in, the system decides how to group them for picking. It builds waves. That means less walking, fewer trips, and more done in less time.
A electronics warehouse doubled their picking rate during peak season. No extra hands. Same team, just smarter paths.
4. Internal Movements
You know those stock moves that seem small but always throw off the flow? EWM handles them quietly. It watches bin levels, triggers replenishments, and keeps pick locations full without anyone having to flag it.
I remember one site saying they had not run an emergency replenishment in months. That used to be a daily thing for them.
5. Labor Management
This part shows you how long tasks take, compared to how long they should take. It is not about pressure. It is about knowing where things slow down and why.
One of our sites used this to spot a pattern in staging delays. Fixed it with a layout tweak. They ended up increasing output by 18 percent without adding people.
6. Quality Management
For sites that need inspections, especially in pharma or food, EWM can block inventory for checks. It will not let expired or failed items move forward until they clear.
One pharma distributor told me they stopped shipping expired stock completely after setting this up. That used to be a big problem for them. Now, it is just handled.
7. Cross-Docking
Sometimes things come in and go right back out. No need to store them. EWM spots those cases and sends the goods straight to outbound.
Retailers normally use this for seasonal stuff. They cut handling costs by 40 percent just by skipping storage for the fast-moving items.
8. Value-Added Services
You can run kitting, labeling, and even light assembly right inside the warehouse. SAP EWM builds work orders for it and tracks what gets used.
One technology brand I worked with, used this to build custom PC bundles. All done inside their DC. It saved them a ton of time, and they stayed flexible with last-minute orders.
9. Mobile Solutions
No more paper pick lists. The system connects to handhelds and scanners. Workers get instructions as they move and confirm tasks right on the spot.
After switching to mobile, one warehouse I supported got their error rate under 1 percent. That used to be a big issue, especially on night shifts.
So, What’s the Real Benefit?
It is not one feature. It is how everything works together. When receiving runs better, putaway improves. When picking is optimized, shipping flows faster. The system catches gaps before they turn into problems.
And honestly, that just makes the day easier. You get fewer surprises. More consistency. And when things go wrong, which they always do, you have the visibility to fix them before they pile up.
That is what SAP EWM really does. It helps you stay one step ahead.
Core Components of SAP EWM
Component | Functionality | Business Value |
---|---|---|
Inbound Processing | Manages goods receipt from vendors, production, or returns; includes unloading and putaway tasks. | Accelerates receiving operations; improves stock visibility immediately upon receipt. |
Outbound Processing | Covers picking, packing, staging, and shipping of goods for outbound deliveries. | Optimizes order fulfillment speed and accuracy, reduces shipment errors. |
Warehouse Structure Management | Defines layout such as storage types, bins, and sections; mirrors physical warehouse setup. | Improves space utilization and simplifies complex warehouse operations. |
Inventory Management | Real-time tracking of stock quantities, movements, and statuses inside the warehouse. | Minimizes stock discrepancies and supports accurate reporting and audits. |
Slotting and Rearrangement | Analyzes product demand and suggests optimal storage locations; reorganizes inventory layout dynamically. | Boosts picking efficiency and reduces travel time inside the warehouse. |
Labor Management | Tracks warehouse worker tasks, productivity, and shift management through defined standards. | Improves workforce planning, boosts operational performance, and supports incentive programs. |
Resource Management | Allocates warehouse resources (forklifts, personnel) based on operational priorities and workload. | Maximizes asset utilization and reduces idle times for equipment and labor. |
Yard Management | Controls and monitors truck movements and dock appointments within the yard area. | Reduces bottlenecks and wait times for incoming and outgoing transport. |
Warehouse Order Creation | Groups tasks into logical warehouse orders for execution by staff or automated systems. | Improves task distribution efficiency and reduces operational delays. |
Material Flow System (MFS) | Connects EWM to automated warehouse systems like conveyors and cranes directly. | Enables high-speed, real-time control of automated equipment without middleware. |
Warehouse Monitoring and Analytics | Provides dashboards, KPIs, and alerts for warehouse activities and exceptions. | Enables proactive management and continuous process improvement through real-time data. |
SAP Logistics and Industry Execution
SAP for Manufacturing
Explore how SAP supports factory operations, warehouse flows, and integration with MRP.
SAP for Retail
Manage store-level distribution, fast-moving inventory, and omnichannel logistics with SAP.
SAP Modules Overview
Understand where logistics, supply chain, and manufacturing modules connect in SAP.
SAP Integration Platforms
How different SAP systems like TM, GTS, and PP integrate across logistics and operations.
Traditional Warehouse Management vs SAP EWM
SAP EWM does more than replace SAP WM. It rethinks the way the warehouse runs. The design feels like it was built by people who actually spent time on the floor. That matters. You can configure processes to reflect how things really happen, not how a system assumes they should.
I have worked with teams that used SAP WM for years. It worked well enough, as long as things stayed simple. But once volume picked up or automation was introduced, gaps started showing. SAP EWM helps close those gaps, especially where flexibility and control are needed most.
If your warehouse is preparing for change, whether that means higher order volume, new automation, or a transition to SAP S/4HANA, then this shift matters.
1. Scalability and Automation Capability
One key difference shows up when warehouses try to scale. SAP WM can only stretch so far. It handles basics well, but it was not built for high complexity or fast growth.
SAP EWM, on the other hand, keeps performance stable even as the workload increases. Larger bin counts, higher order volumes, and tighter fulfillment windows all run smoother.
I supported a facility that introduced pick-to-light and robotics in one of their zones. With SAP WM, those upgrades would have required workarounds. SAP EWM handled it directly. They kept their timelines and avoided extra customization.
Here are a few areas where scalability stands out:
Multiple waves or overlapping picks
Complex replenishment rules
Integration with conveyor systems or robots
That flexibility is useful, especially during seasonal spikes or layout changes.
2. Architecture and SAP Roadmap
There is also the long-term view to consider. SAP WM was built for ECC. SAP EWM was built for S/4HANA. That shift affects more than just IT, it affects how the warehouse fits into the larger business system.
SAP is clearly investing in EWM. Support for WM will eventually phase out. It may not feel urgent today, but delays in migration often lead to rushed projects later. Starting early gives your team time to adjust.
From a supervisor’s perspective, this means fewer disruptions down the road. The system stays updated. Features improve. You keep moving forward without major surprises.
In short, SAP EWM is better aligned with what warehouses need now, and what they will need next. It is a solid step forward. Even if you take it slowly, starting the transition early gives you more room to do it right.
Difference Between Traditional WM and SAP EWM
Feature | Traditional WM | SAP EWM |
---|---|---|
System Architecture | Part of SAP ERP ECC; embedded within logistics execution (LE-WM). | Standalone module or decentralized system on SAP S/4HANA platform. |
Process Coverage | Basic inbound, outbound, and stock transfer processes. | Advanced inbound, outbound, labor management, slotting, kitting, and returns handling. |
Automation Support | Limited; needs third-party tools for automation. | Integrated Material Flow System (MFS) directly connects to conveyors, cranes, robots. |
Resource Management | Manual or minimal resource tracking. | Full labor and equipment resource tracking and optimization. |
Slotting and Rearrangement | Not available. | Dynamic determination of best product placement based on velocity and demand. |
Yard Management | Limited truck handling; manual check-in/check-out. | Full yard management with dock appointment scheduling and yard visibility. |
Flexibility and Scalability | Rigid; difficult to extend for complex warehouse needs. | Highly flexible; easily scales across warehouses, regions, and industries. |
User Interface | Basic SAP GUI screens. | Modern Fiori-based user experience for mobile and desktop operations. |
Integration with SAP TM and GTS | Limited direct integration capabilities. | Native and seamless integration with SAP Transportation Management (TM) and SAP Global Trade Services (GTS). |
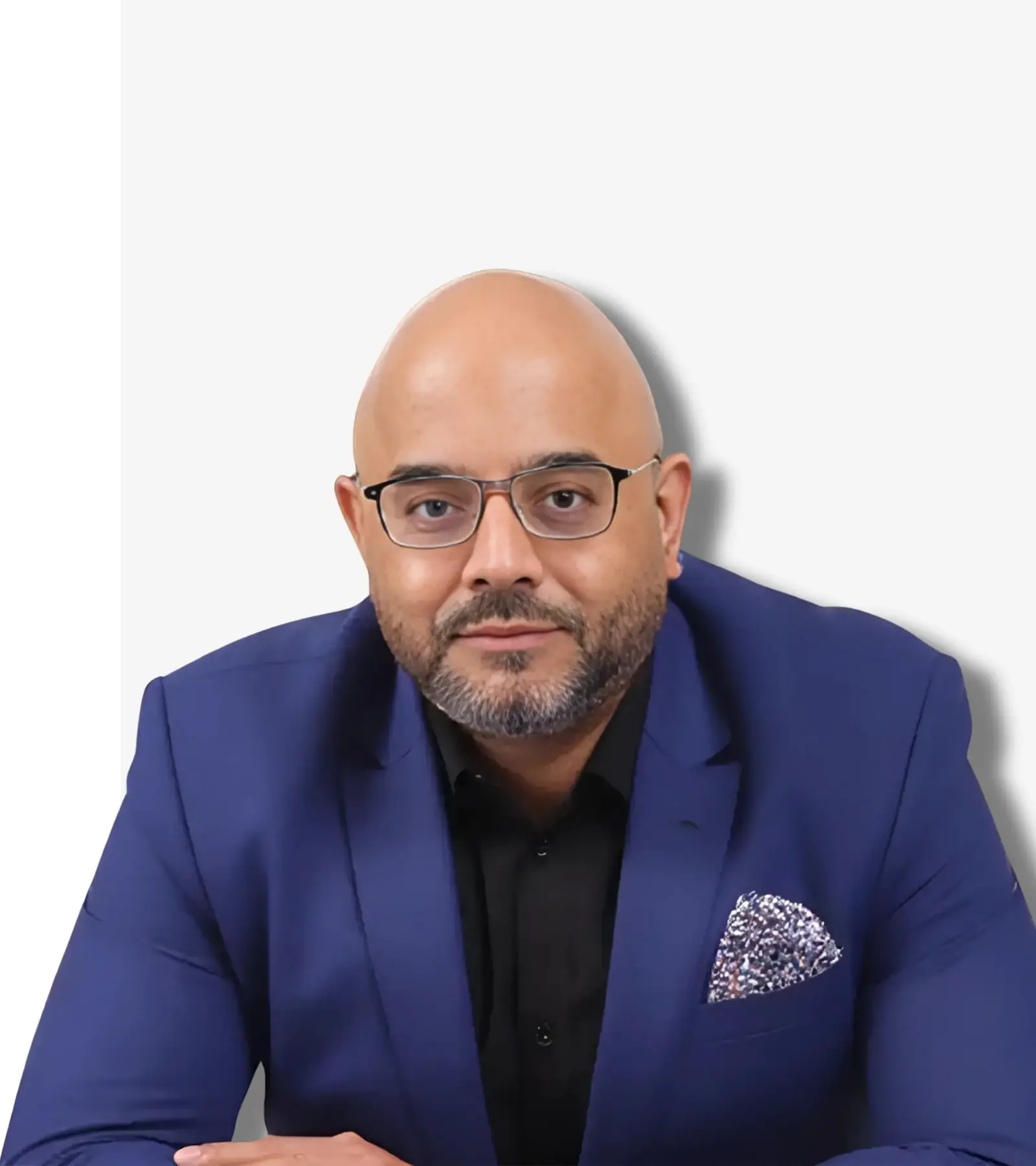
See How I Make Your ERP and AI System Selection or Implementation right for you.
ERP & AI System Selection – Identify and choose the right ERP or AI-enabled platform to fit your business needs.
Project Support & Recovery – Keep your project on track or bring failing implementations back under control.
ERP Modernization – Transform existing ERP systems to modern, efficient, and scalable ERP environments.
GET IN TOUCHStop Losing Money on Outdated WMS
If your warehouse still runs on an older WMS, the gaps are probably showing. Maybe not every day, but often enough to notice. SAP EWM gives you a way to close those gaps. It connects tasks, people, and inventory in a way that feels more aligned with how warehouses actually work.
I have seen setups where workers spend more time fixing system mistakes than doing the actual job. When that starts to feel normal, the system has already failed. SAP EWM handles complexity without slowing things down, which is one reason more warehouses are switching over.
Even if your current system still works, the hidden costs can pile up, slow picks, order errors, and stock that moves but never updates properly. All of that cuts into performance.
1. SAP WM Is Ending…Now What?
SAP WM had a good run. For years, it helped warehouses manage inventory and keep things moving. But it was built for a different pace, in a different era. SAP is now shifting its focus entirely to SAP EWM as part of S/4HANA.
That means no more improvements to WM. Eventually, support ends. So this is not just a software upgrade, it is a business decision. Waiting too long to start that transition can make the switch harder later.
SAP EWM is already being used in warehouses that move thousands of items per hour. It supports automation, custom rules, and live data. If your current system lacks that visibility, every delay becomes harder to explain.
2. SAP EWM vs. Manhattan, Oracle, Blue Yonder
There are other WMS options out there. I have worked with a few of them. Manhattan and Blue Yonder focus more on retail and fulfillment speed. Oracle has a strong cloud WMS, but often feels separate from operations.
SAP EWM stands out when you need deep integration. If you already use SAP ERP, then EWM feels like a natural extension. It fits into production, transportation, and inventory planning without needing extra layers.
Here are a few things to consider during a WMS upgrade:
Can the system handle high-volume operations without custom patches?
Does it scale with automation as you grow?
How well does it integrate with the rest of your supply chain?
SAP EWM gives you more control now, and more flexibility later. That is hard to ignore.
SAP EWM Features That Drive Results
SAP EWM is not just a toolkit. It is a system designed to solve everyday problems that warehouses deal with, missed scans, delays, stock in the wrong place, people waiting on tasks. In my experience, even a small shift to SAP EWM can reduce friction during the day. Sometimes it is just about seeing what is going on, clearly and without delay.
Each feature is built to drive results: time saved, fewer mistakes, and smoother flow. Over time, that adds up.
1. Real-Time Yard and Labor Tracking
One feature that tends to make a big difference is visibility. SAP EWM gives real-time tracking of people and trailers, which helps you make quicker adjustments during the shift. Instead of reacting late, you spot issues before they get worse.
Here’s what I’ve seen in warehouses that track dock assignments and labor activity. They usually spot bottlenecks much earlier. Often sites notice their late-day dock congestion come from a handful of inbound trailers showing up too close together. After making a small change in scheduling, they started finishing earlier, and with less stress on the team.
You also get better clarity on task performance. When the numbers are in front of you, it is easier to shift resources or support the areas that fall behind.
2. Automation and Robotics Sync
As more warehouses bring in automation, the gaps between human and machine tasks become more noticeable. SAP EWM helps close those gaps. It integrates with sorters, conveyors, and even robotic systems, so tasks are better coordinated.
In my opinion, this is where the system starts to show real value. Without it, automation creates new silos. One warehouse I visited had issues with robotic pickers being idle while orders sat in staging. Once they aligned EWM to drive the robotics directly, the flow improved. Fewer delays. Fewer mismatches.
That translated to better use of the equipment, and less idle time across the board.
3. Optimized Slotting, Returns, and Cross-Docking
EWM’s slotting tools help you place fast-moving items where they save the most time. It looks small on paper, but over a full day, it reduces travel paths and speeds up picking. Especially in high-volume zones, that change really adds up.
Returns are also cleaner. Instead of holding items to one side waiting for someone to deal with them, the system quickly identifies what can go back into stock and where it should go.
I’ve seen seasonal operations use cross-docking to avoid extra handling. They receive, stage, and ship, often all in one shift. It keeps products moving and cuts handling costs without requiring major changes to the layout.
Together, these features do more than automate tasks. SAP EWM helps create a warehouse that runs smoother, with fewer unknowns. And for most teams, that makes each shift a little easier to manage.
SAP EWM Sub-Modules: What They Are and Why They Matter
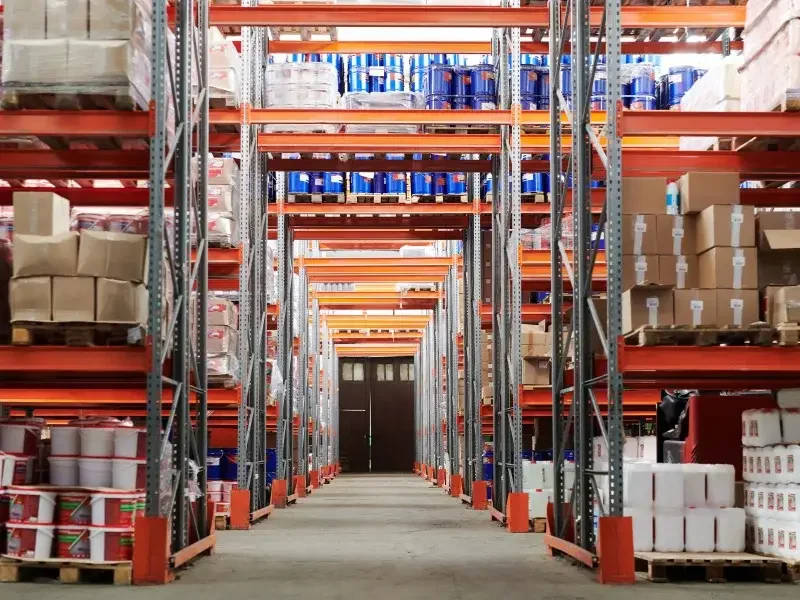
SAP EWM comes packed with specialized sub-modules that handle specific warehouse functions. Let’s break them down.
1. Receiving and Inbound Processing
The SAP EWM module manages everything from yard check-in to putaway. When a truck arrives, the system knows what’s coming and guides the receiving process step by step.
A beverage distributor I worked with reduced their receiving time by 35% by using the Advanced Shipping Notification features. Trucks get unloaded faster, and the yard doesn’t back up anymore.
2. Storage and Operations
SAP EWM handles the heart of your warehouse – where products sit while waiting to be picked. The module manages bin locations, storage types, and stock movements.
What makes it powerful is the storage strategy engine. EWM can automatically decide the best place to store each product based on size, velocity, and storage requirements. One retail client optimized their storage so well they freed up 20% more space in their existing facility.
3. Outbound Processing and Shipping (OPS)
OPS covers everything from order release through shipping. It includes wave management, picking, packing, and loading.
The wave management capabilities let you group orders for maximum efficiency. Instead of picking one order at a time, workers pick multiple orders in a single trip through the warehouse. An electronics distributor doubled their picking productivity during peak season using this approach.
4. Yard Management
SAP EWM tracks trucks and containers in your yard. The system manages dock appointments, tracks which vehicle is at which door, and helps coordinate loading and unloading.
A grocery distributor used this to cut their yard congestion by 40%. They know exactly when trucks arrive and depart, and drivers spend less time waiting.
5. Labor Management
This module tracks productivity and helps manage warehouse staff. The system establishes standard times for tasks and measures actual performance against those standards.
You get clear visibility into who’s performing well and who needs coaching. One consumer goods company improved overall productivity by 18% within three months just by having this visibility.
6. Cross-Docking (CD)
CD identifies opportunities to move products directly from receiving to shipping without putting them into storage first.
A fashion retailer uses this for seasonal items. Products go straight from receiving to outbound, cutting handling costs by 30% for these items.
7. Value-Added Services (VAS)
VAS manages product customization, kitting, and assembly within the warehouse. The system creates work orders for these activities and tracks the materials used.
An electronics manufacturer uses this to customize orders right in the distribution center. They build specific configurations based on customer requirements without disrupting their main operations.
8. Quality Management (QM)
QM handles inspections and quality holds. The system can block inventory for quality checks and only release it once approved.
A pharmaceutical distributor uses this to ensure expired products never reach customers. They’ve eliminated shipping errors related to expiration dates entirely.
9. Physical Inventory (PI)
PI manages cycle counting and full inventory counts. The system suggests which bins to count and when, based on value or turnover.
Most companies see a big reduction in inventory adjustment costs after implementing this module. One distributor cut their annual inventory write-offs by 70%.
10. Slotting
This module optimizes product placement throughout the warehouse. The system analyzes order patterns and suggests the best locations for each SKU.
A home goods distributor reorganized their warehouse based on slotting recommendations and reduced picker travel distance by 28%.
These modules work together but can be implemented separately. Most companies start with core functions like receiving, storage, and outbound, then add others as needed. The modular approach lets you tackle your biggest pain points first without overwhelming your team.
Sub-Modules of SAP EWM
Sub-Module | Functionality | Business Use |
---|---|---|
Inbound Delivery Processing | Manages receipt of goods, unloading, inspection, and putaway tasks. | Improves receiving accuracy and reduces dock-to-stock cycle times. |
Outbound Delivery Processing | Handles picking, packing, staging, and shipping activities for customer orders. | Enhances order fulfillment speed and shipment accuracy. |
Warehouse Order Management | Groups tasks into executable orders for warehouse resources (staff or robots). | Optimizes labor allocation and task prioritization. |
Physical Inventory Management | Conducts cycle counts, annual stock checks, and inventory adjustments. | Improves inventory accuracy and audit compliance. |
Slotting and Rearrangement | Automatically determines optimal storage bin assignments based on product demand and dimensions. | Boosts warehouse picking efficiency and reduces travel distances. |
Labor Management (LM) | Measures workforce performance through engineered labor standards (ELS). | Increases productivity and supports performance-based incentives. |
Yard Management | Controls and monitors truck movements, check-ins, and dock assignments at the yard. | Streamlines yard traffic and reduces transportation delays. |
Value-Added Services (VAS) | Handles activities like labeling, kitting, assembling, and repackaging inside the warehouse. | Enhances product customization and supports customer-specific services. |
Material Flow System (MFS) | Direct interface between EWM and automated equipment like conveyors and cranes. | Enables real-time control of automation without middleware layers. |
Cross-Docking | Moves goods directly from inbound receipt to outbound shipping without long-term storage. | Reduces handling costs and shortens delivery lead times. |
Proof It Works – Customer Wins

SAP EWM may look complex at first glance, but the real value becomes clear once it is in place. Many warehouses that adopt SAP EWM start to see improvements quickly, not just in speed, but in consistency and accuracy. In my view, what stands out most is not just what the system can do, but how it adjusts to different types of operations.
These are not theoretical gains. They are based on actual projects where logistics teams worked through real challenges and saw measurable results. Here are a few examples that help put that into perspective.
1. Nadro – 24% Faster Distribution with SAP EWM
Nadro, a major pharmaceutical distributor in Mexico, needed to move product faster through their network. Their legacy WMS could not keep up with the volume, and manual handoffs created frequent slowdowns.
After switching to SAP EWM, they were able to tighten control of inbound and outbound flows across multiple DCs.
What went well:
System visibility helped teams adjust shifts in real time
Directed putaway reduced dock congestion
Faster turnaround on delivery orders
What caused friction early on:
Staff needed time to adjust to system-guided workflows
Initial rule setup was too generic, had to refine putaway logic
2. Komplett – Scaled Fulfillment by 3x
Komplett, a high-volume electronics retailer, struggled with order spikes. During sales events, their existing setup created picking delays and staging overflow. The team was working hard, but output kept falling short.
SAP EWM allowed them to optimize wave planning and adjust pick paths to meet demand.
What went well:
Tripled order capacity during peak periods
Reduced average pick time per order
Slotting adjustments made the packing area flow better
What needed work:
Early wave rules were too rigid for same-day orders
Teams needed tighter training on exception handling
3. Hasco – Robotics + EWM Cut Errors by 40%
Hasco integrated robotics into their warehouse to improve throughput. At first, the coordination between robots and staff created more confusion than speed. SAP EWM helped streamline that interaction, aligning the flow of tasks across both.
What went well:
Error rate dropped by 40%
Inventory updates synced in real time with movement
Task confirmations became smoother with handhelds
What delayed results:
Robotics had to be reconfigured to follow EWM sequences
Some legacy processes clashed with the new task logic
Each site had different goals, but the core idea stayed the same: better coordination leads to fewer problems. SAP EWM helped these teams work faster without losing control. When the system does more of the planning, the floor has fewer surprises. And that tends to make a real difference.
The Hidden Risks of SAP EWM No One Talks About

Let me share some of the real challenges I’ve seen companies face with SAP EWM implementations. It’s not all smooth sailing, and knowing the potential issues that can save you major headaches.
1. Implementation challenges are pretty common.
I worked with a consumer goods company that tried to implement every single feature at once, big mistake. They got overwhelmed and the implementation grinded to a halt.
The successful implementations I’ve seen, take a phased approach, tackling core functionality first and then adding more complex features later.
2. Integration with legacy systems can be a real pain to deal with.
One manufacturer I consulted for had an ancient conveyor control system that wasn’t designed to talk to modern software. We ended up having to build custom middleware just to get basic communication working.
If you’ve got older equipment or systems, plan for extra time and budget for integration work.
3. User adoption is often the biggest hurdle.
Warehouse staff who’ve been doing things the same way for years will naturally resist change. I remember a distribution center where workers were secretly keeping paper records because they didn’t trust the system.
Good training and involving key users early in the design process makes a huge difference.
4. Data migration has caused some real nightmares.
A retail client tried to migrate years of inventory data without proper cleansing, and the errors completely messed up their go-live.
Take the time to clean your data before migration, it’s worth it.
5. Configuration complexity catches many companies off guard.
EWM has thousands of settings and parameters that need to be aligned with your business processes. One wrong setting can cause major issues downstream.
I always recommend working with experienced consultants who can guide these decisions.
6. Performance issues can crop up, especially in high-volume operations.
A high-velocity e-commerce warehouse I worked with had to completely rethink their server infrastructure after experiencing slowdowns during peak periods. Make sure your technical infrastructure can handle the load before you go live.
Choose the Right SAP EWM Deployment

Getting started with SAP EWM involves more than just picking the software. The real work begins when you figure out how it should fit into your operation. I have seen teams dive straight into configuration workshops without first asking where EWM will sit, or how the business plans to scale from there. That part catches up fast.
SAP EWM gives you options. That flexibility helps, but it also means your early choices carry weight. Especially if you’re managing multiple DCs or need room to expand later.
1. Cloud vs. On-Premise – What Fits Your Model?
This usually comes up early, sometimes even before process mapping. Do you want SAP EWM running in the cloud, or hosted on your own infrastructure? The answer depends on what kind of control you need, how fast you want to scale, and how tightly your IT team manages upgrades and downtime.
Cloud-based EWM (public or private):
You can roll it out faster across multiple locations. There is no need to stand up new servers or deal with VPN headaches.
The upfront cost is lower. You avoid the hardware spend and ongoing server maintenance.
System updates happen in the background. So you’re always on the latest release without scheduling big upgrade windows.
If your ERP already runs in the cloud, this keeps things clean and easier to sync.
But there are a few things to weigh:
Custom integrations can be harder to manage. You might need middleware or third-party tools to connect certain systems.
You’ll want strong IT coordination. Since everything runs through the broader SAP landscape, one weak link can cause system lag or availability issues.
On-premise EWM:
You have complete control over performance and behavior. That can be helpful in busy or complex DCs.
Legacy equipment is easier to support. Older scanners or interface hardware usually hook in more easily.
It’s often preferred in regulated environments where data privacy or audit trails are strict.
But keep this in mind:
You’re responsible for everything, backups, patches, uptime.
Upgrades need planning. You’ll need test environments, change controls, and time to validate compatibility.
2. Embedded, Decentralized, or Hybrid?
Once you pick where EWM will run, the next step is how it connects to your SAP core. There are three main routes here, each with its own impact on operations.
Embedded EWM (within SAP S/4HANA):
You get one system for warehouse and ERP. That reduces complexity and keeps master data aligned.
It’s usually faster to implement and easier to manage, especially for a single-site operation.
Best when your processes are tightly tied to ERP flows like production or finance.
Decentralized EWM (runs separately):
Good fit for larger or faster operations where system load could affect performance.
If ERP ever slows down or needs patching, the warehouse can keep running.
Lets you set up different rules across sites without risking conflicts in the ERP.
Hybrid models:
These mix both types. Some sites use embedded EWM for simpler tasks, while the main DCs rely on decentralized systems.
That gives you flexibility during rollout. You can test new features at one site without affecting the rest.
From what I’ve seen, the right choice depends on how your warehouse actually runs, not just what the system is capable of. If your team moves fast, handles lots of exceptions, or shifts product between sites, that will shape your setup more than anything in the spec sheet.
SAP EWM can stretch to fit most models. The key is making sure it fits the way your operation already works, and builds on it from there.
SAP Project Planning and Execution
SAP Project Planning & Control
Methods to manage deadlines, control budgets, and correct off-track SAP initiatives.
SAP Cost Breakdown
A breakdown of hidden costs that can affect large projects like EWM and TM deployments.
Start Your SAP Project Right
Early-stage planning guidance for SAP implementations to avoid future rework.
SAP Budget Planning
Practical steps to allocate project funds, prioritize scope, and manage partner costs.
What Does SAP EWM Cost?
SAP EWM is not priced like a plug-and-play app. It’s a strategic system, and its cost reflects that. Most warehouse teams I’ve worked with come into it expecting an investment, but many still underestimate how much setup, licensing, and customization add up.
Still, SAP EWM pays for itself when you factor in long-term labor savings, accuracy improvements, and throughput gains. The key is knowing where your cost will land and why.
1. What Drives the Price Tag?
A few core factors shape what you will end up paying:
Warehouse size and process complexity
Smaller sites (under 25,000 square feet) with light customization can expect total project costs around $250,000 to $400,000.
Mid-size DCs with 50–100 users and some automation typically range from $600,000 to $1.2 million.
Large or multi-site networks with high automation, custom rules, or robotics can exceed $2 million, especially if run across multiple geographies.
Automation level
Connecting EWM to automated equipment (e.g., conveyors, AGVs, pick-to-light) adds integration and testing time.
Budget 20–40% more if your site includes any material flow systems or advanced automation.
SAP licensing
Basic EWM (included in some S/4HANA licenses) covers standard warehousing.
Advanced EWM requires additional licensing, expect roughly $300–$600 per user per year, depending on contract terms and user volume.
From what I’ve seen, even teams that spend more up front usually recover it within two years. It’s not just the software, it’s the process discipline that comes with it. Fewer lost pallets, tighter inbound visibility, and better labor tracking make a real difference.
If you treat SAP EWM like a long-term operational platform rather than a cost center, the math usually works out.
Solve These Warehouse Problems with SAP EWM
Most warehouse teams I’ve worked with do not spend their day talking about systems. They talk about what broke, what ran short, and how much time got lost chasing something that was supposed to be simple.
That’s where SAP EWM makes a difference. Not in theory, not on a whiteboard, on the floor. It helps solve problems that show up in every shift, especially when volume picks up or space gets tight.
It is not about bells and whistles. It is about reducing the noise so people can just do their jobs.
1. Inaccurate Inventory and Missed Orders
It always starts the same way. Someone picks against a list, gets to the bin, and there’s nothing there. Now the order’s short. Maybe the customer waits, maybe the loader gets blamed. Either way, time’s gone.
SAP EWM helps clean that up:
It tracks every movement, receiving, putaway, picks, transfers.
It flags wrong counts early, before they spread downstream.
It keeps bin-level visibility live, not locked in a spreadsheet from last week.
One ops lead I know said their mis-picks dropped by half, just by getting real-time inventory back under control.
2. High Labor Costs, Low Output
You can add more people, but if the floor plan’s a mess or nobody knows what to do next, things still slow down. I’ve seen teams walk extra miles per shift, not because they want to, but because the system sent them zigzagging.
SAP EWM helps teams move better:
It builds task lists based on zones, workload, and priorities.
It cuts down walking with smarter pick paths and fewer backtracks.
It gives supervisors a view into where time goes and where it gets stuck.
Some sites find they get more done with the same crew. Others reassign labor where it’s needed most, because they can actually see the gaps.
3. Stockouts and Overstocking
Too little stock means delays. Too much means you’re out of space, or money is tied up. Either one drags the warehouse down.
SAP EWM makes stock planning more stable:
It can trigger auto-replenishment when bins dip too low.
It helps slot fast movers closer to pick zones.
It improves tracking on returns and inbound, so nothing sits forgotten.
One manager told me, “For the first time, I trust what the system says is actually on the shelf.” That’s what confidence looks like.
Should You Migrate Data from SAP Warehouse Management to SAP EWM?
This question comes up a lot. I will address this important question based on my experience on this topic.
What Data Can Be Migrated?
- You can move master data like materials, vendors, customers, and warehouse structure. SAP has tools for this.
- SAP WM and SAP EWM are built differently. EWM has more complex storage options. Bins, handling units, and processes work differently.
- Companies that attempt to migrate everything tend to have major issues and end us redoing most of it anyway.
Transactional Data: No
- Don’t move transactional data from SAP WM to SAP EWM. This means open deliveries, transfer orders, inventory documents, and movement history.
- Moving transactions just creates problems. The data structures don’t match up.
- Even SAP does not recommend this approach.
Clean Slate Benefits
- Starting fresh lets you redesign how your warehouse works. You don’t have to copy old processes.
- A consumer goods company redesigned their warehouse layout completely. Their picking speed went up by 30%.
- You also get rid of bad master data. Some SAP WM systems have locations nobody uses, wrong bin assignments, and outdated material data.
What To Migrate?
- Move material master data, but clean it first. Delete obsolete materials and fix dimensions.
- Get customer and vendor data from your ERP system, not SAP WM.
- For warehouse structure, usually better to redesign than migrate.
Hybrid Approach
- Many projects move cleaned master data but redesign warehouse structures and processes.
- This keeps good information while making improvements.
Recommendation
- Use the hybrid approach. Move clean data but redesign what needs to be better.
- SAP EWM gives you a chance to improve your warehouse. Don’t waste it by copying your old system.
What to Migrate (or Not) from SAP WM to SAP EWM
Area | Migration Status | Notes |
---|---|---|
Storage Bins and Types | Partially Migrated | Warehouse layout must be redefined using EWM-specific structures and master data. |
Inventory Data | Migrated | Quant-level inventory must be migrated to EWM; stock balances need validation. |
Open Transfer Orders | Not Migrated | Must be processed or closed in WM before cutover; not transferable into EWM. |
Warehouse Control Unit Interface (WM-LSR) | Replaced | Replaced by Material Flow System (MFS) in EWM for automation integration. |
Putaway and Picking Strategies | Redefined | EWM uses more advanced strategy options; rules must be recreated. |
Handling Unit Management (HUM) | Migrated | Handling units are compatible but need adjustment to EWM-specific HUM settings. |
Custom Z-Reports and Developments | Selective Migration | Re-evaluate relevance; EWM has built-in reporting and warehouse monitoring tools. |
Yard Management Data | Redefined | EWM has a separate Yard Management module; setup differs from WM logic. |
Physical Inventory Settings | Migrated | Inventory procedures need review, but stock counts and statuses transfer to EWM. |
Capacity Checks | Enhanced | Capacity checking must be adapted to EWM’s flexible rule-based architecture. |
Plan Your Move – SAP EWM Migration Guide
Moving to SAP EWM can feel like a big shift, especially if your current WMS has been in place for years. But with the right steps, the transition becomes less of a leap and more of a walk forward. Most teams I’ve seen succeed did not try to fix everything on day one. They planned for the long haul.
SAP EWM offers better control, better data, and a system that grows with you. But to get there, you need to line things up first.
Here’s what usually works:
1. Audit Your Current Setup
-
Walk the floor. See how your current WMS supports daily tasks, and where it falls short.
-
Map out what is custom, manual, or duct-taped together. Those areas matter most during migration.
2. Define the Right Scope
-
Start with one site or flow. Make it manageable.
-
Focus on what creates the most delay or risk, usually inbound, picking, or stock accuracy.
3. Create a Steady Go-Live Plan
-
Build in time for testing, training, and small mistakes. They will happen.
-
Set check-ins after go-live. Adjust based on what actually happens, not just what was forecast.
Most of all, keep it practical. SAP EWM works best when it fits your real process, not the other way around.
Conclusion: The SAP EWM Journey
SAP EWM changes warehouses. It replaces paper with scanners. Manual processes become automated. Guesswork turns into data-driven decisions.
The system isn’t perfect. Implementation takes time and money. Change management challenges pop up. But companies who push through see real benefits.
Inventory accuracy improves. Labor costs drop. Customer service gets better. The warehouse becomes a competitive advantage instead of a cost center.
For companies still using WM or other legacy systems, the question isn’t if you should upgrade to EWM, but when and how. The gap between basic and advanced warehouse management grows wider every year.
What’s your warehouse story? Have you implemented EWM or are you considering it? What challenges have you faced in your warehouse operations?
Share your experiences in the comments below. Tell us what worked, what didn’t, and what you wish you’d known before starting. Your insights might save someone else a lot of headaches.
Do you need support in your business? Feel free to message me directly if you have specific questions about your situation.
Questions You Might Have...
1. What is SAP EWM used for?
SAP EWM is used for managing complex warehouse operations. It handles all warehouse processes from receiving to shipping. Companies use it to control inventory movement, optimize storage locations, manage picking and packing, coordinate yard activities, and integrate with automation equipment. It’s designed for warehouses that need more capabilities than basic inventory management.
2. Is SAP EWM part of S/4 HANA?
SAP EWM comes in two versions. There’s a basic version embedded within S/4 HANA that handles simpler warehouse needs. Then there’s the full standalone version (decentralized EWM) for complex warehouses. The embedded version has fewer features but integrates seamlessly with S/4 HANA. The standalone version offers all features and can connect to S/4 HANA or older ERP systems.
3. Which is better SAP MM or SAP EWM?
This isn’t an either/or question – they serve different purposes. MM (Materials Management) handles purchasing, inventory valuation, and basic materials tracking. EWM focuses specifically on physical warehouse operations.
Most companies use both: MM for procurement and inventory accounting, EWM for actual warehouse operations. They work together as part of a complete supply chain solution.
4. Is SAP EWM in high demand?
Yes, SAP EWM consultants are in high demand right now. Many companies are upgrading from older warehouse systems or implementing EWM for the first time. The move toward automation and complex fulfillment operations drives this demand. The job market is particularly strong for consultants who understand both the technical side and warehouse operations.
5. What is the salary of SAP EWM consultant?
SAP EWM consultants typically earn between $85,000 and $140,000 base salary depending on experience and location. Entry-level consultants start around $85,000 while senior consultants with 5+ years of EWM experience can earn $120,000 or more. Independent consultants often charge $100-150 per hour. Consultants who understand both EWM configuration and warehouse operations command higher rates.
6. What does EWM stand for?
EWM stands for Extended Warehouse Management. The “Extended” part distinguishes it from SAP’s older, simpler Warehouse Management (WM) module. It’s called “extended” because it goes beyond basic inventory tracking to include advanced capabilities like wave management, labor management, and automation integration.
7. Is EWM part of ERP?
EWM can be part of ERP but often runs as a separate system. The embedded version comes included with S/4 HANA ERP. The decentralized (standalone) version runs separately but connects to your ERP through interfaces. Large warehouses typically use the standalone version for better performance and more features, while smaller operations might use the embedded version.
8. What is the benefit of SAP EWM?
The main benefits include higher inventory accuracy (typically 99.5%+), increased labor productivity (15-30% improvement), reduced shipping errors, better space utilization, and the ability to manage complex warehouse operations. EWM also provides real-time inventory visibility, supports automation equipment, and offers detailed analytics for warehouse performance. Most companies see a return on investment within 12-24 months after implementing EWM.
9. What is the job role of SAP EWM consultant?
SAP EWM consultants analyze warehouse needs, configure the system to match business processes, test warehouse scenarios, train users, and support go-live activities. They translate business requirements into technical configurations. The role requires understanding both warehouse operations and SAP technology. Consultants need to configure storage strategies, work with process orders, set up RF devices, create warehouse dashboards, and integrate EWM with other systems.
10. What is the future of SAP EWM?
The future looks strong for SAP EWM. SAP continues to invest in the product with quarterly updates. Recent development focuses on cloud deployment, integration with automation equipment, AI-driven slotting optimization, and improved analytics. As more companies adopt automation and robotics in warehouses, EWM’s role becomes more important. SAP has made it clear that EWM remains their strategic warehouse platform for the foreseeable future.
11. What is the function of SAP EWM?
SAP EWM manages the complete flow of materials through a warehouse. Key functions include receiving, put-away, internal movements, picking, packing, shipping, and yard management. It also handles slotting optimization, labor management, quality inspection, cross-docking, and value-added services. The system directs all warehouse activities, tracks inventory in real-time, and provides analytics for management decision-making.
12. Who can learn SAP EWM?
Anyone with supply chain background or SAP experience can learn EWM. Ideal candidates include warehouse supervisors, logistics managers, other SAP consultants (especially MM or WM), and supply chain analysts. Learning EWM requires understanding warehouse operations first, then the technical aspects. No specific programming knowledge is required, though some configuration tasks involve complex rules. Most people need 2-3 months of training and hands-on practice to become proficient.
13. Who uses SAP EWM?
Large and mid-sized companies with complex warehouse operations use SAP EWM. This includes manufacturers, distributors, retailers with distribution centers, third-party logistics providers, and wholesalers. Industries like automotive, pharmaceuticals, electronics, food and beverage, and retail frequently implement EWM. The system is especially popular in companies handling high volumes, managing multiple warehouses, or dealing with complex fulfillment requirements.
14. What are the key features of SAP EWM?
Key features include:
- Flexible storage bin management
- Wave planning and execution
- Labor management and monitoring
- Yard management
- Cross-docking
- Integration with material handling equipment
- RF (radio frequency) device support
- Slotting optimization
- Picking and packing strategies
- Quality management
- Value-added services management
- Kitting and assembly
- Resource management
- Warehouse analytics and KPIs
- Integration with SAP TM (Transportation Management)
Each of these features helps optimize different aspects of warehouse operations, from space utilization to labor efficiency.